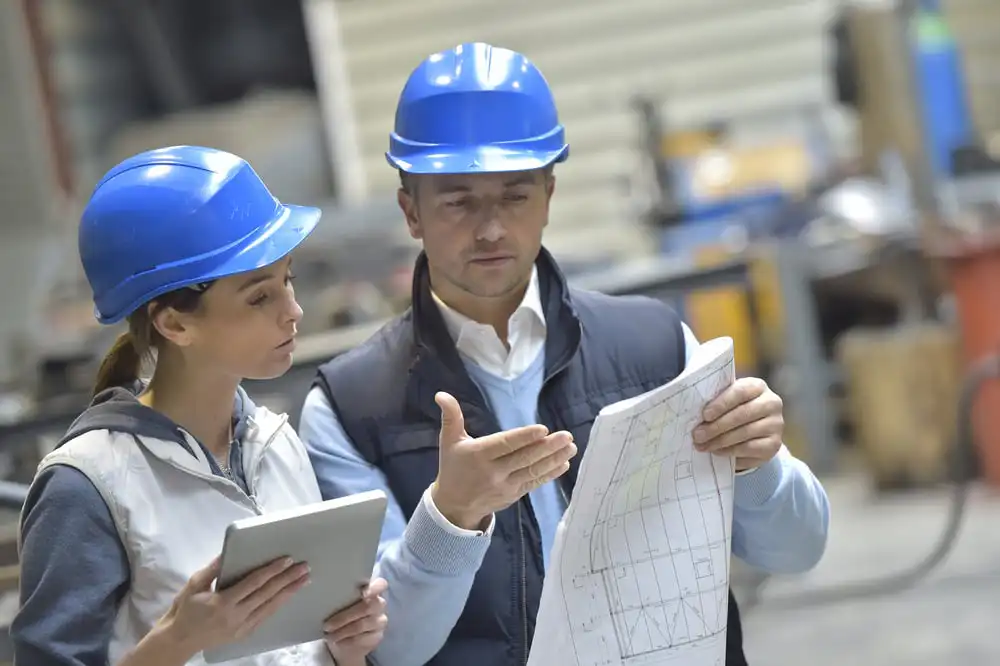
‘In with the new’ doesn’t have to mean ‘out with the old’.
With RS Industria’s manufacturing improvement service, useful data can be quickly and easily extracted from both new and legacy machines. This flow of collective data enables users to monitor critical assets, in real time, and make better decisions to reduce production losses.
Most factories feature a mix of legacy machines, operating side-by-side with more modern equipment. One production line could be 37 years old and another just 18 months, with both performing similar roles.
To ensure all these processes (old or new) are running optimally, the manufacturing leader needs to identify any operating losses, and – by collecting and analysing data – find solutions that will eliminate or mitigate their impact. From high energy costs to high emissions, amount of waste, unplanned downtime and production yield, the continuous monitoring of factory processes is key to alleviating your biggest industrial pain points.
Ongoing condition monitoring of industrial processes isn’t new. What is new, however, is the tools that enable you to do this much quicker and more efficiently. While much has been made of ‘Industry 4.0’ or the ‘Industrial Internet of Things (IIoT)’, in simple terms it’s about using technology to rapidly collect and analyse large data sets coming from various processes in the factory.
This real-time data enables better decision-making. For instance, if a machine is getting too hot or generating excessive vibration, the real-time data captured from that machine will alert the user to take action.
It might be something as simple as a part needing to be cleaned or adjustments made to the lubrication. But the sooner it is dealt with, the less likely a problematic failure will occur, preventing costly downtime. Maintenance then becomes a proactive, preventative measure rather than a break-fix initiative.
How do you blend old and new assets with an IIoT solution?
While IIoT does rely on sensors and smart devices to get data out of these processes, adopting an IIoT strategy does not mean purging old equipment.
An IIoT strategy should harmonise your equipment, irrespective of age. In fact, RS Industria actively encourages manufacturers to use its modular IIoT platform to first unlock data that already exists inside legacy equipment, before rolling the solution out to other assets.
This modular approach is what makes RS Industria different to other condition monitoring solutions on the market. We don’t want you to blindly extract the maximum amount of data possible; we want you to see and digest the insights that you will find most useful, then grow to other assets in a controlled and manageable way.
The challenge, however, is that your machines are all set up differently and ‘talk’ different data languages (for example, OPC-UA, MODBUS or PROFINET).
Nevertheless, RS Industria’s secure Edge Gateway can collect that data and translate all the languages into one common format, before securely transmitting it to a cloud application that provides users with a single point of insight.
“We’ve invested in the technology to make it easy for the user to get access to their existing data,” explains Richard Jeffers, Founder of RS Industria. “We have a whole host of device libraries and translation files, which means that if we plug an ethernet cable into the side of the device, we can read the data and translate it so that it can generate useful information for the user.”
How can data insight make your older equipment more efficient?
Existing data (which was previously dormant and unused in your assets) can be leveraged to solve multiple problems.
Take energy consumption, for example. Measuring electric consumption through an electric motor can reveal how much power is being consumed. If it’s monitored over a period of time, trends will soon appear relating to whether the motor is running efficiently.
If the energy consumption is going up, it indicates that there is a fault.
Using data that already exists can provide other insights, too. For instance, a company recently approached RS Industria to help it extract data from its legacy machines to reveal any losses with regard to performance, availability, and quality.
“Once they had the fact-based information, they could then use this data to make better decisions,” says Jeffers. “If you don’t have that robust data then you run the risk of tackling the wrong problem.”
These data-led decisions could also result in the replacement of legacy machines. Very few machines fail because of end-of-life; they are replaced because the data reveals that they are no longer cost-effective to run in terms of maintenance and energy consumption.
Once users have reaped the benefits from their first installation of RS Industria, they can then move into phase two.
As a modular platform, RS Industria allows existing data to easily be enriched with new data coming from a larger range of assets.
We’re brand agnostic and can connect a variety of PLCs, automation systems and sensors to our solution. Additionally, we manage the entire connection and configuration procedure on your behalf, saving time for your busy maintenance and production teams.
No matter which asset you choose to start with, RS Industria can help you to uplift your processes by unlocking the hidden information that has been stored in your machinery – releasing new-found insights to boost operational performance, reliability, and sustainability.
Ready to learn more?
Read on to ‘Case Study: Reducing Energy Usage Through Insight at Kerry’.