- Case Study -
How RS Industria drove down a leading food producer’s energy consumption by 14%
Kerry Foods is part of Kerry Group, a global leader in taste and nutrition. Its Worcestershire-based Tenbury Wells site produces sweet and fruit ingredients, including preserves, fillings, sauces, and toppings.
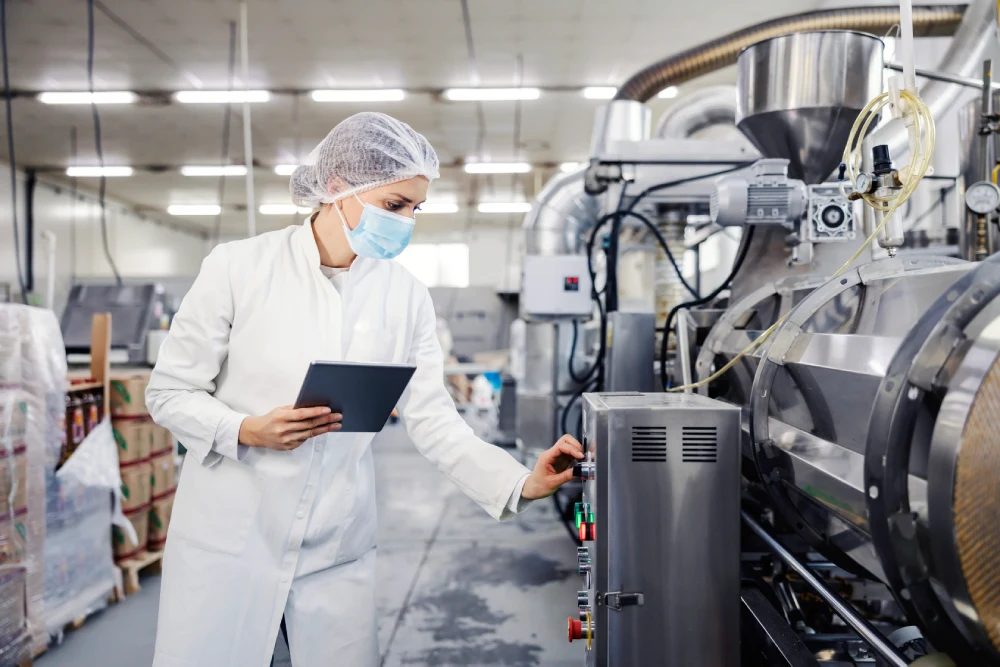
The Benefits
Reduced
Consumption
Lowered energy usage by 14% within weeks, representing a huge step toward corporate sustainability goals.
Positive
Behaviours
Influenced workforce behavioural change around energy saving.
Real-time
Data
Enabled valuable insight into consumption leading to targeted energy-saving initiatives.

Easy and
Affordable
RS Industria is a quick and simple solution, with no significant capital for the customer required.
0%
Reduction in site energy consumption within just a few weeks
0
Tonnes of CO2 saved per year

The Problem
Kerry Group is committed to achieving Net Zero before 2050 and working to reduce emissions across its operations by 2030.
In response to its over-arching factory sustainability goals, and against a backdrop of soaring energy costs, Kerry Foods’ Tenbury Wells site was challenged to make meaningful energy savings.
However, with little insight into how and where energy was being used, energy efficiency projects were difficult to implement.
The Solution
By leveraging the power of RS Industria, the Kerry team was able to understand how and where energy was being used at the site, and how they could reduce consumption without affecting production volumes.
Though the Tenbury site had some existing energy sub-meters positioned downstream from the main incomer, consumption data had to be manually collected weekly and was of limited use.
By connecting these existing submeters to the RS Industria network and installing new sub-meters in other key locations and production lines, RS Industria provided Kerry’s engineers with a clear picture of where energy was being used – on a realtime basis.
The Outcome
RS Industria has enabled the customer to reduce energy consumption by 14% – in just four weeks.
With energy consumption broken down by asset, process, location, and time, detailed insight revealed high areas of waste that could be immediately rectified, such as equipment left on standby over weekends or when not in use.
By shifting maintenance work to weekday night shifts, consumption of heat and lighting at weekends was significantly reduced, generating more savings than the cost of the nightshift labour.
With energy usage of individual lines now available, combined with the cascade of insight into sitewide consumption, an energy-saving culture was created amongst staff, who have since made further changes to operating procedures to maximise
energy savings.
"RS Industria enabled us to connect all our existing meters…very quickly, we were able to get a comprehensive view of how we're using our electricity by hour, by minute, by second, across the site.”
Ben Botwright, Engineering Manager
Next Steps
RS Industria is already in use at the Tenbury site’s wastewater treatment plant, where the insight generated from the system has enabled engineers to reduce freshwater consumption, cut effluent disposal costs and automate essential measurements to ensure the site remains environmentally compliant.
Kerry engineers are also now in the process of rolling out RS Industria to measure and monitor fuel and water consumption and steam output of the site’s two fuel-oil-fired boilers, which will unlock further energy savings.
Related Blogs
How data insight helped a food manufacturer tackle rising energy prices and hit the road to Net Zero
Seven ways RS Industria saved a leading food manufacturer time and money
Revolutionising Time, Cost Savings for Food Manufacturers
"We've been able to influence perople's decisions and behaviours, by giving them basic information"
Ben Botwright, Engineering Manager