The Benefits

Real Time Asset Monitoring
Vibration sensors continuously monitor refrigeration compressors, enabling condition-based maintenance.

Early Detection
of Issues
Abnormal vibrations on compressor No.3 were detected, allowing for timely maintenance, preventing a potential breakdown and
production loss.

Enhanced Maintenance
Planning
Real-time data allows for forward maintenance
planning and continued controlled use of critical assets.

User-friendly
System
Straightforward and easy to use, with support from RS Industria solutions engineers.
0T
Potential waste product savings
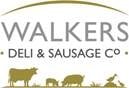
The Problem
For food manufacturers, the chilling and freezing plant is key to production and F&B industry compliance.
Walkers’ site is home to four refrigeration compressors, which are used to cool a number of blast chillers. This ensures products are kept fresh and that a compliant chill chain is maintained.
If all the blast chillers are in use, three compressors are required. However, due to the critical importance of chilling in maintaining production, the site has a
backup in the event of failure with an additional fourth compressor.
This approach proved its worth when one of the compressors failed and had to be replaced.
With a two-month delivery lead-time for the new compressor, the remaining three would be in continuous use.
Acutely aware of their potential exposure to another breakdown that could seriously affect production, and with limited insight into the condition of the remaining compressors, site engineers needed a quick, innovative, and affordable solution that could continuously monitor asset performance and avert potential issues.
The Solution
The modular build, flexibility, and resulting insight offered by RS Industria made it the ideal solution. RS Industria’s solutions engineers worked closely with Walkers’ site team to tailor the best approach.
Vibration sensors for each compressor were located on the compressor heads and drive motors, which enabled the customer to receive detailed vibration information on bearings and drive shafts.
The resulting data means the site’s engineering team can now continuously monitor performance in real-time and use the insight to plan for condition based maintenance.
The Outcome
Within hours of the installation, an abnormal level of vibration was detected on the drive motor of one of the compressors.
While it meant the asset wouldn’t fail immediately, engineers were able to closely monitor the compressor for any further degradation while they waited for the new compressor to be delivered.
Once the new compressor was installed, engineers could take the faulty compressor offline for maintenance and repair, while keeping it onsite and available as a backup for the other compressors should it be required.
Had the asset failed, the consequences would have been costly for the customer, with the product within the line at the time of failure being thrown away and the compressor out of action for a significant period of time.
"I think the system is really easy to use, it has been the easiest to pick up of a number of systems.”
Liam Cope, Engineering Specialist
The Lessons
Until the installation of RS Industria, Walkers had limited insight into the condition of their refrigeration compressors.
Next Steps
Now, with the detailed continuous data provided by the platform, they can run condition-based maintenance on these critical assets. For the site engineers, the data has proved to be useful and, in their own words, has delivered value from day one. Indeed, the insight has proved so valuable other areas of the business have expressed an interest in using RS Industria to monitor the reliability of the packing lines, ovens, and another set of refrigeration compressors, and exploring its potential use to reduce energy costs.