Case Study: Reducing Energy Usage Through Insight at Kerry
3 min read
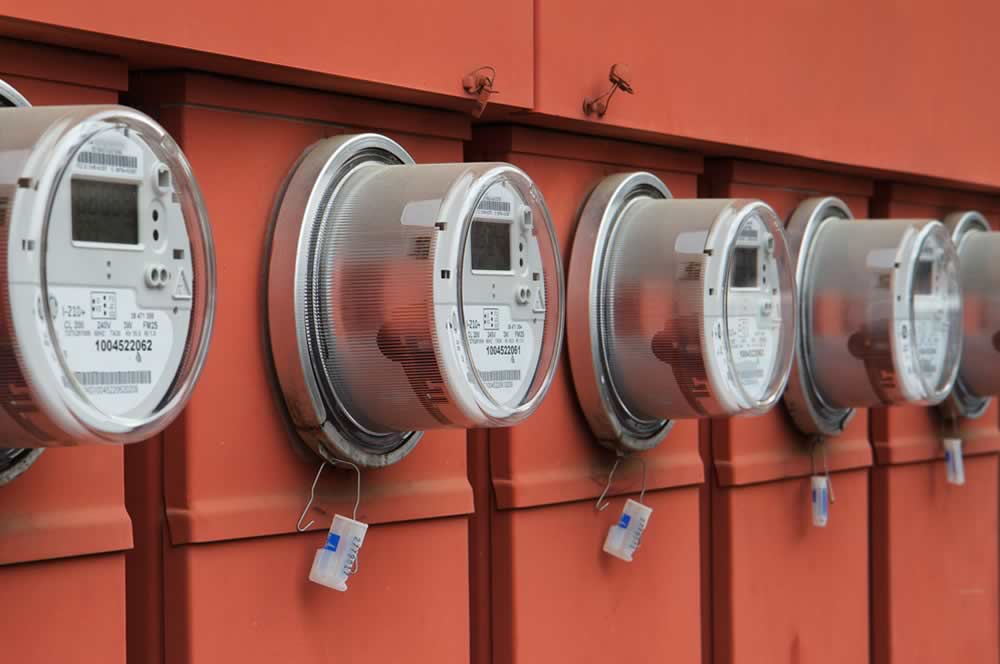
Like most manufacturers, Kerry is keen to reduce its energy consumption.
Implementing RS Industria’s manufacturing improvement service revealed real-time insights, and in a matter of weeks, the company achieved a 14% reduction in energy usage.
The Challenge
Soaring energy costs as a result of surging oil and gas prices are having a huge impact on our economy, especially in highly energy-intensive industries such as manufacturing.
Keeping factories running amid constantly rising energy prices is challenging. It’s a difficulty all too familiar to manufacturers such as Kerry - a global leader in the development of taste and nutrition solutions for the food, beverage and pharmaceutical markets.
Its Tenbury Wells production site, part of the Sweet and Cereal division, was keen to make meaningful energy savings. This wasn’t just to reduce costs, but to meet its corporate commitments to sustainability.
However, without understanding how and where energy was used, it was difficult to know where to optimise consumption.
The Solution
The answer to gaining much-needed understanding of energy consumption lay in IIoT.
Kerry had already installed the RS Industria platform at its wastewater treatment plant (WTP) for compliance monitoring. By digitally connecting both legacy and new equipment to a cloud-based monitoring system, the engineers were able to gain real-time insights from a continuous stream of operating data. As a result, the site managed to reduce freshwater consumption by up to 100,000 litres per day.
Having gained such significant benefits, the Tenbury site decided to extend its use of the RS Industria platform into energy usage. Being a modular platform, this was simple, fast, and affordable to do.
The Journey
Existing energy sub-meters were connected to the RS Industria network, together with new sub-meters that were installed in other key locations and production lines.
From this data, key insights were gained. For instance, it revealed that as much energy was being consumed during the weekend shutdown as a normal production weekday. The reason being that heating and lighting were kept on over the weekends for any maintenance that had to be carried out.
The data also unveiled that the many items of production equipment left on standby when not in use were actually consuming almost as much energy as when they were in use. They also uncovered several ‘hidden’ processes and items of equipment that were running unnecessarily but had not been visible in terms of energy consumption.
With these insights, the Kerry team were able to understand their specific use of energy.
Armed with this information, they could now act and start to reduce consumption without affecting production volumes.
This resulted in a series of all-new actions and benefits:
- Equipment items identified as big consumers of energy were completely turned off when idle.
- Maintenance work was moved from weekends to weekday night shifts. The weekend energy savings easily covered the additional nightshift labour cost.
- Energy consumption information was shared with relevant staff, who soon got onboard with this new energy-saving culture and changed their operating procedures to maximise energy savings.
- A multi-disciplinary energy-saving task force was quickly established to find further quantifiable savings, with a number of staff from operations, maintenance, H&S and finance actively involved.
- The energy content of individual product lines was then calculated for the first time.
The Outcome
“The RS Industria platform enabled us to connect all our existing meters relatively easily, and we were able to add some additional ones,” explains Ben Botwright, Engineering Manager at Tenbury. “Very quickly we were gaining a comprehensive view of our electricity usage by hour, by minute, by second across the site.”
Some incredible results were experienced within weeks of implementing the RS Industria solution.
Key amongst these was a 14% reduction in energy usage.
This reduction in energy not only cut Kerry’s electricity bills but also reduced the site’s output of CO2 by 60 tonnes every year.
This helped in progressing the site towards achieving its corporate sustainability goals.
Tenbury’s staff responded very positively to having this real-time consumption data, so much so that another key benefit of the platform was that it resulted in major workforce behavioural change around energy saving.
“Having data to be able to influence people’s decisions and behaviours and make improvements is fantastic,” says Botwright. “The benefit of the Industria system is that you can see the impact of any changes very quickly.”
Botwright and his team are planning to further extend their use of RS Industria’s modular platform to begin measuring and monitoring the site’s two oil-fired boilers. By accurately measuring both fuel and water consumption, as well as the output of steam, the hope is that these insights will lead to even further energy savings.
RS Industria enables you to optimise energy use and show precise consumption profiles, providing the information needed to immediately discover possible savings.
Additionally, for an unmatched 360° view, you can import online utility accounts or access several online utility metres.
As well as revealing energy-saving actions, RS Industria gives you access to leading-edge digital tools, which support continual asset improvement - as well as continuous support from RS experts and specialist services.
We’ll help you to achieve your sustainability goals.
Making the transition from broad corporate aspirations to specific eco-friendly actions can be difficult.
Where do you start? How can you prioritise?
Our service helps manufacturers improve energy efficiency by providing real-time data insights and identifying areas for improvement. By optimising energy use, manufacturers can also enhance their overall competitiveness by becoming more resource-efficient and even reducing waste.
Ready to learn more?
Read on to ‘7 Tips to Avoid Data Hacking at Your Factory’.