CNC Machines
A CNC (Computer Numerical Control) machine is a type of automated tool that uses pre-programmed computer software to control the movements of tools and a platform.
Since any particular component might require the use of several different processes (cutting, drilling, milling, and routing), modern machines often combine multiple tools into a single ‘cell’.
CNC machines are used to reliably produce components to a high degree of accuracy and tolerance, and they have revolutionised machining processes in manufacturing industries including aerospace, automotive, medical, and electronics, to produce complex parts and components with tight tolerances.
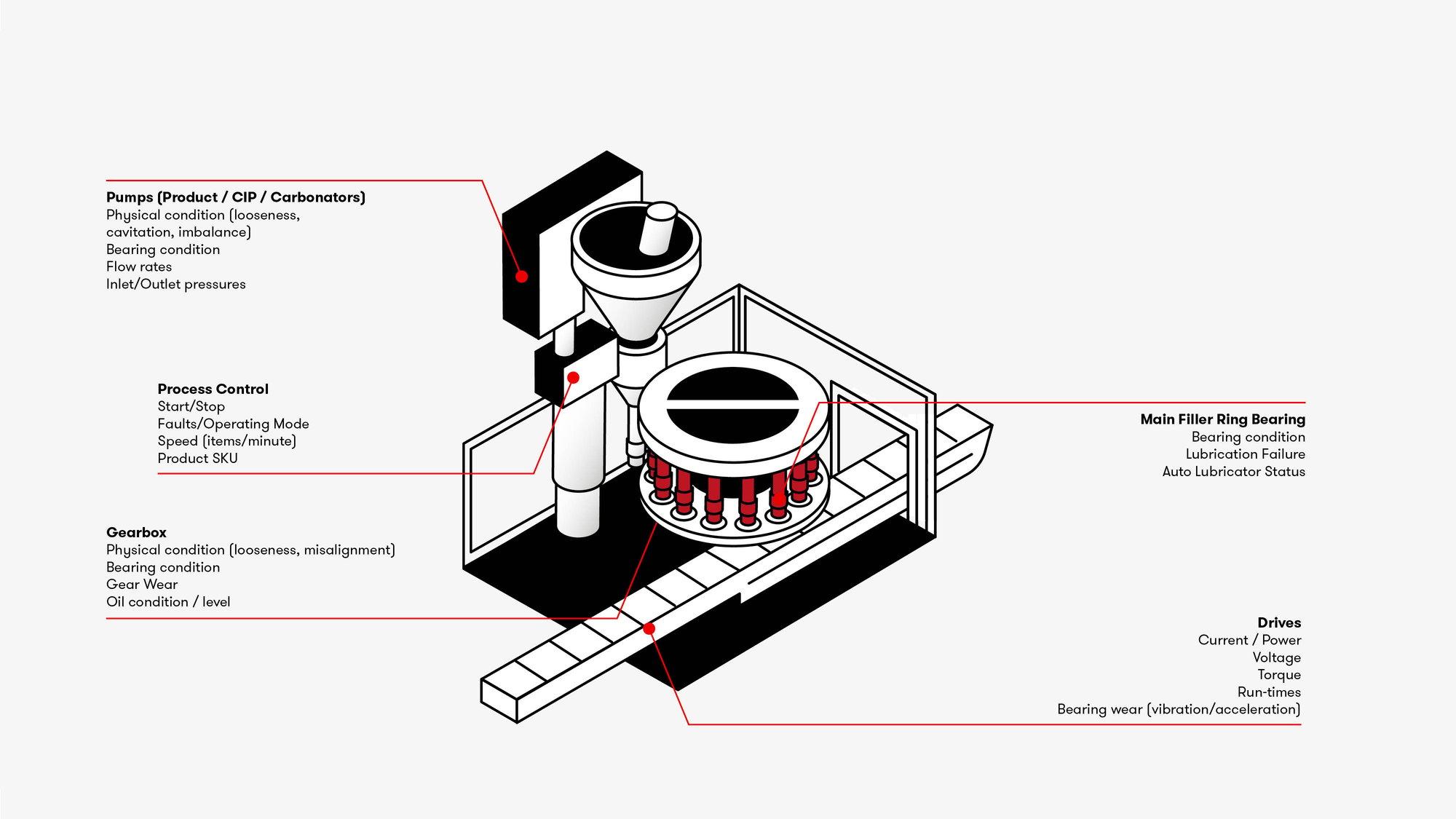
Overview
Combining computer technology with mechanical and electrical components to automate the manufacturing process, CNC machines are extensively utilised in mass production and consumer goods manufacturing - offering precision, efficiency, and versatility.
With the help of RS Industria, your CNC machines can provide even greater value to your production cycle. By unleashing the previously untapped data in your assets, you’ll have the insight required to improve the performance of your critical machinery, leading to increased uptime and even shrinking your carbon footprint.
Energy Consumption
The Challenges
CNC machines are often large power-hungry machines, with intermittent operating periods. It can be difficult to monitor energy consumption over time, leading to potential energy losses going unnoticed.
Our Solution
If no electrical consumption data is available, then energy meters can be easily installed which can pass data direct to RS Industria.
Your Benefits
Using our data and the insight from the machine process, the site can then start to quantify the energy cost on the asset and understand any energy wastage. You can also look at the energy consumption variations related to product type, for more accurate costings.
Book an Energy Consultation to find out how much you could save!
Operations
The Challenges
Incorrect tool setting for the current workpiece and task will cause issues with the CNC machine performance and the resulting quality of product. Operator or programming induced errors can cause delay and ultimately lead to machine damage where incorrect usage puts excessive loading on the CNC machine toolset and drive mechanism.
Our Solution
Online monitoring of a CNC machine’s setup, using process data from the controller unit, can help manufacturers identify operational errors and inconsistencies in setup. Furthermore, online condition monitoring can help identify wear and tear, allowing pre-scheduled maintenance before issues becomes critical.
Increasing overall operational efficiency can be achieved by preventing in-service breakdowns and mitigating any equipment availability issues. In addition, improvement in cycle times for component manufacture can be made by identifying inefficiencies in the process.
Your Benefits
CNC machines are complex and expensive assets critical in the component production process, any unplanned downtime can cause delays in production. Mitigating against these losses can have a significant improvement in the asset’s operational efficiency.
The cost of downtime will depend on the type of work and the level of machine usage, but a recent survey by the IMechE estimated downtime to cost an average of £5,000 per hour.
Maintenance
The Challenges
The physical condition of the main drive motor, gearbox and spindle of a CNC machine has an impact on the efficiency and overall reliability of the asset. During machining, the spindle arm of a lathe is subjected to high variations in both overall load and thermal condition. The significant forces created by the milling or cutting process are transferred to the spindle bearings, which can be a cause of failure and subsequent downtime losses.
While physical inspections can find certain issues with the machine, underlying issues in hidden objects such as bearings and gearboxes cannot always be seen and can result in a failure during production. Early detection of these hidden problems is possible with continuous vibration or electrical drive monitoring.
Our Solution
CNC machines operate at high speeds and with high precision, which puts a lot of stress on their mechanical components. Predictive maintenance requires the continuous monitoring of the relevant leading indicators of failure - over all the operating modes.
By using continuous monitoring, rather than relying on intermittent monitoring or manual inspection, the risk of maintenance-induced failure is eliminated. Our solution uses a wired vibration system that collects data continuously, capturing operating data through all machine operations, loading conditions and speeds - along with any transient events which may occur. We couple this data with machine controller data to build a detailed operational profile of the asset.
By monitoring the vibration levels of a CNC machine, it’s possible to detect potential issues before they cause a breakdown or decrease the machine’s performance. This can help reduce maintenance costs, increase productivity, and improve the reliability of the machine.
Your Benefits
RS Industria immediately detects changes in asset condition and can then create warning alerts, allowing early corrective action that will return the CNC machine to a healthy state.


Increase Efficiency

Reduce Downtime
Gain Asset Insight Now
Find out how we can help lower energy usage, enhance reliability and improve operational performance: in a way that is simple, fast and affordable.
Book a Demo