The Role of Outsourcing in Maintenance Engineering
2 min read
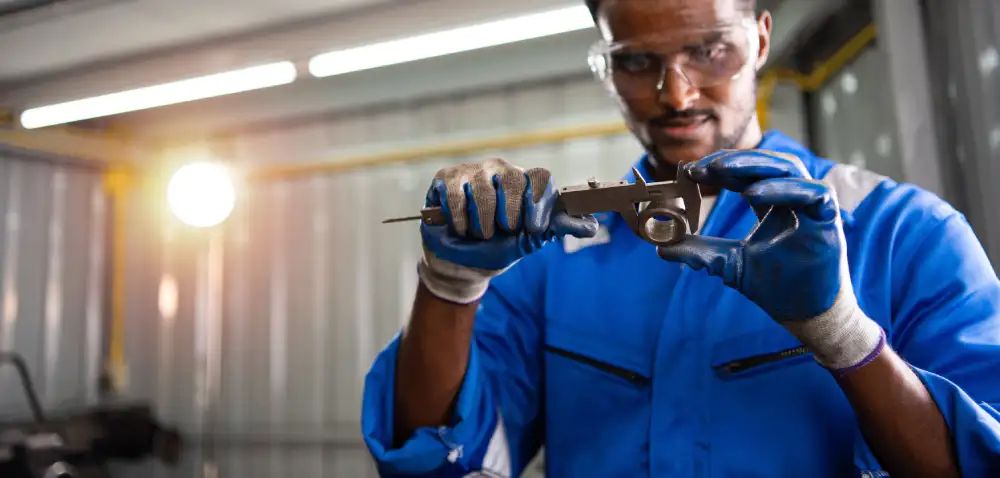
What are the benefits of outsourcing maintenance engineering and is it the right choice for your organisation?
A recent survey of maintenance engineers by RS and the Institution of Mechanical Engineers (IMechE) reveals that more than a third of respondents work in organisations that do not currently outsource any maintenance processes. Moreover, only one in ten of these said they would consider outsourcing in the next six to twelve months.
The same survey, the results of which are shared in Industry in Motion: Maintenance Engineering Report 2023, also reveals the many benefits that outsourcing offers ¬¬– benefits that those who eschew this option are missing out on.
Here we explore what these advantages are and offer expert advice on how to pursue outsourcing. First, though, we consider the drivers behind the decision to outsource.
What and why?
Which maintenance functions are candidates for outsourcing? Asked what they would consider getting external providers in for, survey respondents state predictive maintenance technology (50%), energy loss surveys (35%) and lubrication services (31%).
Why not undertake these tasks in-house? Survey respondents who have already outsourced some maintenance services mention reduced headcount (35%), lack of skills among staff (40%) and too many specialised skills being required (57%).
The initial motivation behind outsourcing is a lack of internal resources
While this indicates that the initial motivation behind outsourcing is a lack of internal resources, the maintenance engineers who have gone down this route report a range of benefits that weren’t on the original list of reasons. Their top five are cost effectiveness and flexibility (32% each), overall efficiency (28%), reduced probably of failure and decreased downtime (26% each).
These are meaningful gains, almost as significant as the results generated by the highest priority maintenance strategies. Survey respondents list their maintenance strategy priorities as planned (25%), predictive (15%) and energy management (14%) and describe the advantages they offer in strikingly similar ways to the benefits of outsourcing. Cost effectiveness again comes out top (52%), followed by decreased downtime (41%), reduced probability of failure (35%) and better productivity (35%).
Tackling challenges
What difference does this make on the ground? Take decreased downtime as an example. According to the findings shared in Industry in Motion, the biggest drivers of unscheduled downtime are ageing assets (28%), mechanical failure (18%), lead time to get hold of product (11%) and operator error (10%).
Maintenance engineers want to reduce the amount of unscheduled downtime within their plants
With the average hourly cost standing at £5,121, it is unsurprising that maintenance engineers want to reduce the amount of unscheduled factory downtime within their plants. They plan to achieve this by upgrading equipment (48%), widening monitoring capabilities (46%), improving training (38%) and introducing a preventative maintenance strategy (33%).
The latter is the most common candidate for outsourcing too. As noted above, half of survey respondents said they would consider using external providers for predictive maintenance technology. As also noted above, one of the biggest benefits of outsourcing is decreased downtime, which more than a quarter describe as one of its advantages – making it a great way to address a costly challenge.
How to decide
If you’re uncertain whether outsourcing is the right choice for solving an issue in your operations, Richard Jeffers, Managing Director of plug-and-play Industrial Internet of Things (IIoT) platform RS Industria, has three rules to guide decision making.
“First, outsource if it’s genuinely cheaper – which is not that often,” he says. “Second, it can be a good way of coping with peaks and troughs in demand. And lastly, it can make sense if you need a specialist skill that you either don’t have, or don’t wish to have, in house.”
“Whatever you do needs to fit the strategic needs of the business”
Dr Moray Kidd, maintenance engineering academic
Maintenance engineering academic Dr Moray Kidd agrees. “Whatever you do needs to fit the strategic needs of the business,” he advises. “For example, organisations that are specialists in providing services including condition-based maintenance are probably best-placed to take on, or support, the maintenance of high-risk or critical equipment.”
“A hybrid approach works really well,” he adds. The benefits of outsourcing reported by survey respondents suggests they’d concur.
For more on how outsourcing can support your strategic maintenance goals, check out our article that explores the question “How much is downtime costing you?”