How Much is Factory Downtime Costing You?
3 min read
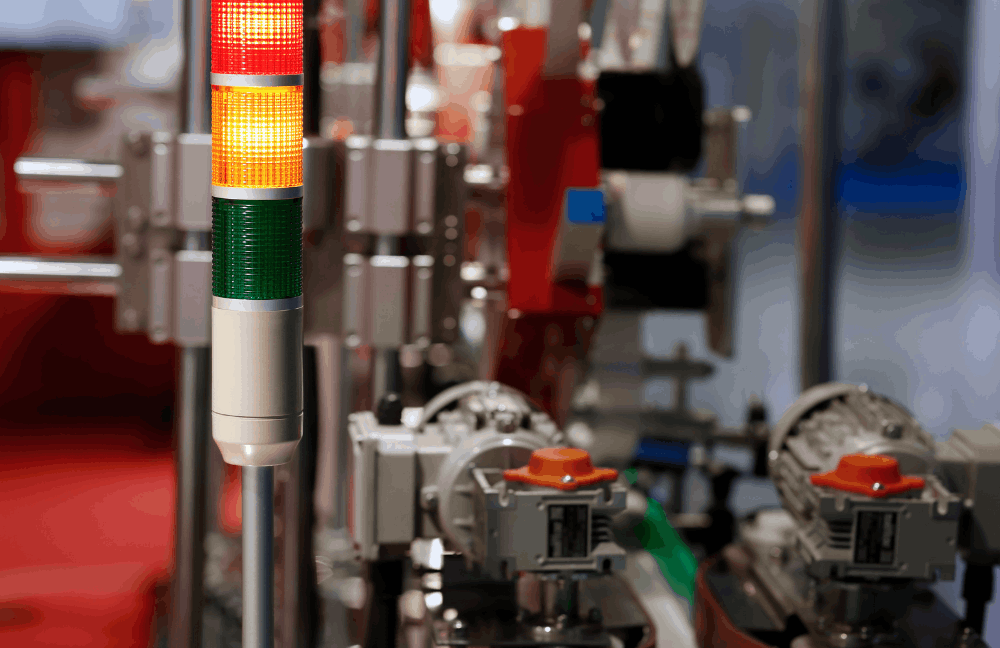
Reducing manufacturing downtime is a high priority for maintenance engineers.
“Downtime is the biggest challenge facing maintenance engineers in our survey,” states a new study, Industry in Motion: Maintenance Engineering Report 2023, produced by RS and the Institution of Mechanical Engineers (IMechE).
Those working in the profession may not be surprised by this finding. What may be more of a shock, however, is just how costly downtime is for UK businesses.
Reducing factory downtime can be a daunting challenge, but you don't have to face the problem alone. Here we share the statistics from the report before exploring how maintenance engineers are tackling this issue...
Time equals money
According to the survey of IMechE members that forms the basis of the Industry in Motion report, maintenance engineers spend 18.3 hours per week on scheduled maintenance. They spend even more time on unscheduled maintenance – 19.6 hours per week, to be precise.
The survey generated figures for the financial implications of this downtime. Eighteen hours of scheduled maintenance translates into an average weekly cost of £93,700, while almost twenty hours of unscheduled maintenance comes in at an average of more than £100,000.
The average cost per hour of downtime is £5,121
At an hourly level, the average cost of downtime is £5,121, although that number disguises the level of variation. The size of the company makes a big difference, with an hour of downtime costing less than £500 for 39% of the smallest firms and more than £10,000 for 24% of large firms.
The causes of downtime
The biggest driver of unscheduled downtime is ageing assets (28%), followed by mechanical failure (18%), lead time to get hold of product (10%) and operator error (10%). The role of the latter needs more recognition, argues Richard Jeffers, Managing Director of RS Industria, a plug-and-play Industrial Internet of Things (IIoT) platform.
Source: Industry in Motion: Maintenance Engineering Report 2023
“A lot of downtime is incorrectly ascribed to maintenance”
Richard Jeffers, Managing Director, RS Industria
“A lot of downtime is incorrectly ascribed to maintenance” says Jeffers in the report. “Your line might be down because you have got a failed component which is clearly a maintenance problem, but if the operators are putting damp card into the packing line carton erector, that’s also going to cause downtime.
“If you just look at downtime and blame it all on maintenance, you are going to draw the wrong conclusion. You’ve got to understand what is an availability issue – the machine not being available when it’s needed – and what is a performance issue, such as a machine that’s not running at the correct speed.”
Aim for less not none
Despite this caveat, unplanned maintenance is still an issue. It is also one that cannot be eliminated, says maintenance engineering academic Dr Moray Kidd. “Despite working for over 20 years with predictive and condition-based maintenance, this remains a huge challenge,” he explains. “It comes back to resources, the right people, the right number of people and sufficient time and planning.
“There’s been a lot of progress in preventative maintenance scheduling, but that’s led to incredibly demanding maintenance schedules.”
These tight schedules can be easily disrupted. “Even with some of the best maintenance practices I’ve seen, there’s always a horror story at some point where something went badly wrong and needs to be fixed,” adds Kidd.
“I think there will always be unscheduled maintenance”
Dr Moray Kidd, maintenance engineering academic
“That puts additional pressures on already limited resources – and I don’t see that going away anytime soon. Absolutely, there should be an aim to continuously reduce this, but in my lifetime, I think there will always be unscheduled maintenance.”
Factory downtime reduction strategies
Despite not being able to eliminate unscheduled maintenance completely, many in the profession remain committed to reducing factory downtime as much as possible. More than 40% of respondents report decreased downtime as one of the benefits of their highest priority maintenance strategy, trumped only by cost effectiveness (52%).
A third of engineers want to introduce a preventative maintenance strategy
They are pursuing a range of strategies to achieve this goal. Almost half are planning to upgrade equipment and a similar number are looking to widen monitoring capabilities. Improved training is also popular, while a third want to introduce a preventative maintenance strategy.
Outsourcing is part of their approach too. More than a quarter who use a maintenance service regard reduced probability of failure and decreased downtime as major benefits. Emma Botfield is Managing Director, UK and Ireland, at RS and attributes this success to collaboration between suppliers and customers, comparing the relationship to that of patient and GP.
“It’s about understanding what you are trying to achieve”
Emma Botfield, Managing Director, UK and Ireland, RS
“They don’t just give you a solution. They try and diagnose what your problem is first, what’s causing you the pain,” she says. “That’s where a real trusted supplier can work with you because it’s not about a transaction. It’s about understanding what you are trying to achieve and where are your pain points and jointly solving them to deliver the best value for money for your organisation.”
As one of the biggest pain points of all, downtime is a prime target for such joint solutions.
Discover how perceptions of digital transformation among maintenance engineers can obscure changes within the industry in our article “Is Digital Transformation a Myth?”