High-Speed Rotary Fillers
Engineered for the efficient and accurate filling of food and beverage containers, fillers help to ensure that the correct amount of product is dispensed every time - ensuring consistency on your production line.
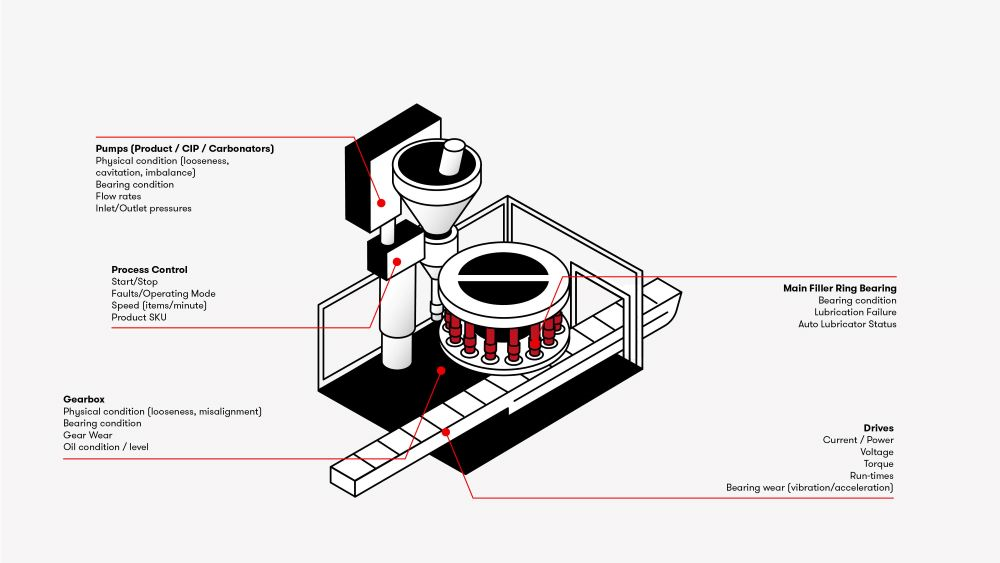
Potential Savings Using RS Industria
£0
Potential Savings in Energy Costs
£0
Reduction in Downtime Costs
£0
Savings in maintenance costs
Overview
High-speed beverage packaging lines are complex machines often costing tens of millions of pounds. The most expensive and critical asset on the line is usually the rotary filler.
At the core of the filler is the main ring, which picks up the bottles, cans, or containers and rotates them into the filling station and through the closure mechanism. Depending on the container type, this can be a crown capper, screw top, or can lid seamer.
Energy Consumption
The Challenges
Sustainability is a key driver in the beverage industry, with engineers keen to understand the consumption behaviours of their machines. With better insight, companies can implement energy optimisation strategies and reduce operational costs.
Our Solutions
RS Industria uses the data already typically available within the variable speed drives and panels to capture energy consumption at the point of use. If this is not available, RS Industria leverages metering solutions to capture data, which allows energy use to be quantified.
Book an Energy Consultation to find out how much you could save!
Your Benefits
Using data from the process, you can start to quantify the energy cost of your filler and understand where wastage is occurring, with the ability to drill deeper into consumption variations related to product type or speed changes. By leveraging the power of RS Industria, you can also identify wasted energy from the over-operation of components such as pumps and drives.
£3,500 Energy Annual Savings
Operations
The Challenges
Filling machines play a significant role in the food and beverage sector, with the Overall Equipment Effectiveness (OEE) of the whole line normally calculated from this asset. Breakdowns, changeovers, shortstops, and speed loss can heavily impact the performance and availability of the line, whilst short fills rejected after the filling stage will impact quality.
The machine operator can control many aspects of the machine, which will affect the size and scope of production losses, as the filler moves away from its operational centreline.
Our Solutions
By collecting data directly from the control system PLC, RS Industria can build a picture of how the asset is operated by gathering process and operational data such as machine speeds, product size, run times, and process stage.
This will enable accurate operational recording and inform issue resolution. Where PLCs are not used or their data is inaccessible, a separate data collection unit can be fitted to mirror existing control signals.
Your Benefits
RS Industria provides a better understanding and greater visibility of machine operation, creating insight into its performance through different products and cycles. This can also highlight how the machine’s operation influences its reliability.
£2,000 Operations Annual Savings
Maintenance
The Challenges
For engineers maintaining high-speed fillers, the main challenge is usually around limited machine access, with some running 24/7 and only stopping for 6-8 hours per fortnight.
Ensuring that engineering resource is used effectively during that period is critical. While inspections can find certain issues with the machine, underlying issues in hidden components like bearings and gearboxes cannot always be seen, potentially leading to eventual failure during production.
Our Solutions
Predictive maintenance requires the
continuous monitoring of the relevant leading indicators of failure over all the operating modes across both production and
CIP (cleaning in place).
RS Industria uses a wired vibration system to continuously collect data through all processes and speeds, along with any transient events which may occur. By coupling vibration data with machine data such as speed, product, and container, RS Industria builds a detailed operational profile of the filler.
Implementing continuous monitoring rather than relying on intermittent monitoring or manual inspection eliminates the risk of maintenance-induced failure, saving you time and money.
Your Benefits
Reducing the risk of unplanned failure is key in an industry where 24/7 availability is required.
RS Industria can help detect changes in condition and trigger early warnings so that corrective action can take place to repair the asset. If the asset cannot be returned to its optimum state, then RS Industria can provide early warnings that account for the lead times for replacement parts, reducing the MRO spend until needed.
Using RS Industria’s continuous condition monitoring solutions and carrying out maintenance once alerted to issues reduces the risk of any secondary damage to the machine, allowing the site to move from a reactive to a planned maintenance strategy.
£10,000 maintenance Annual Savings


Increase Efficiency

Reduce Waste
Eradicate Your Production Line Blues
Find out how we can help lower energy usage, enhance reliability and improve operational performance: in a way that is simple, fast and affordable.
Book a Demo