Why predictive maintenance is a way of life
4 min read
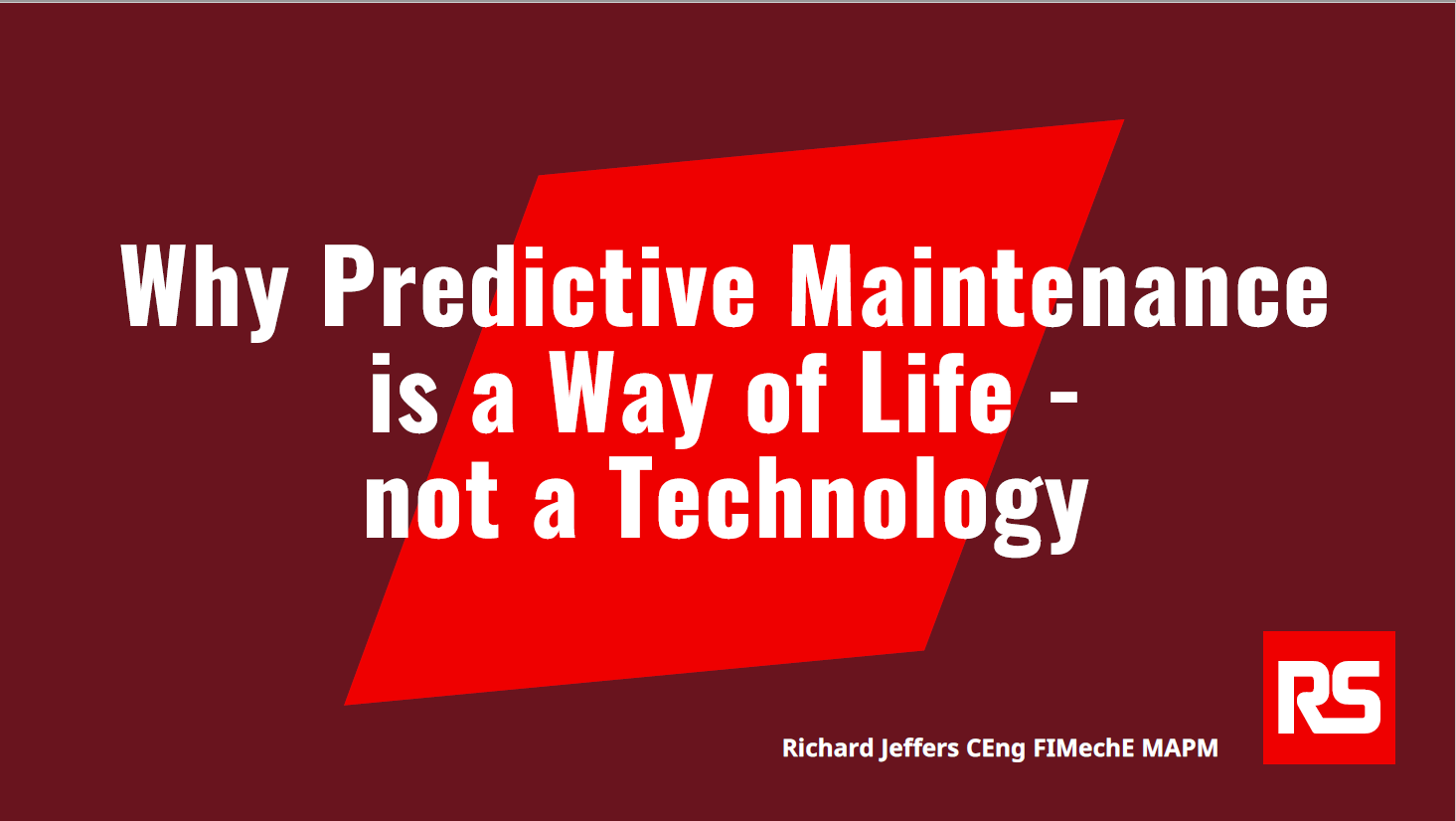
The Managing Director of RS Industria explains why predictive maintenance about culture change as much as digital technologies
“Culturally, we were failing,” said Richard Jeffers, Founder and Managing Director of RS Industria, a modular Industrial Internet of Things (IIoT) platform, talking about an incident earlier in his career in maintenance engineering. “We’d done the right stuff, we’d measured the right thing, but utterly failed to take action based on that measurement activity.”
Jeffers was addressing a packed keynote theatre at the recent Maintec conference, part of the suite of events that made up Manufacturing and Engineering Week at the NEC in Birmingham. During his talk, Jeffers shared questions that asset managers need to ask themselves to determine the right maintenance approach for their facilities and emphasised the importance of cultural change within organisations, illustrating this with examples from RS Industria customers.
Here are some of the highlights from his speech.
Establishing the right approach to maintenance
As an asset manager, how do you start thinking about the right maintenance approach to take?
There are five real questions you’ve got to ask yourself. The first one is what’s the state of my assets? And what state do I want to keep my assets in? You’ve got to think about what assets are critical to sustaining improvement or what subsystems are critical for sustained improvement?
You’ve got to look at your different sub-assemblies or different components in your line and go which ones do I really, really care about because I’m going to spend more money, more predictive maintenance, more condition monitoring on those assets.
You’ve got to think about investment strategies because run-to-fail is a perfectly legitimate strategy. When you’re looking at your assets, you’ve got to think is it a repair strategy? Is it a replacement strategy because it’s end-of-life where the cost of maintenance is higher than the cost of investment? Or is it a major rebuild or regeneration strategy where I can do a smaller investment of Capex and extend the life of this asset by potentially additional years?
Last of all, and this is important for why predictive maintenance is a way of life, not a technology, I’ve got to think about my organisational capability to deliver this because I can have the best maintenance strategy in the world but if I’m not executing on the ground then it’s of no use to me.
Safety and savings with predictive maintenance
People start off with the reactive fix-it-when-it-fails approach and you move through into your planned approach then into your predictive approach. Ultimately, when you enter your enterprise-centred maintenance approach, you’re looking at the total lifecycle of maintenance and the total impact on the supply chain.
There’s a perception in many organisations that [reactive] is cheap and [predictive] is expensive, but the reality is very different.
[With reactive], you’ve got a high cost of spares because you’re constantly replacing things that you don’t need to replace. You’ve got a high cost of labour because you’ve got to have technicians set like coiled springs, ready to leap into action.
You’ve got a high cost of finished goods because you can’t rely on your supply chain. You’ve got to protect your customers with stock rather than a reliable plant. You’ve got high operational and safety risks as the most dangerous thing you’re going to do in most manufacturing sites is invasive reactive maintenance. If you’re relying on that, you are introducing significant safety challenges.
When you’re in the predictive world and into reliability-centred maintenance, it appears expensive because you’ve got to invest to get there. But once you’re there, you’ve got a low cost of spares because you’re only replacing components when they’re about to fail, not because they’ve reached so many hours. You’ve got a low cost of labour because you’re now scheduling the activity. You don’t need those cold springs anymore, waiting to leap into life.
You’ve got low cost of finished goods and you can drive working capital out of your entire supply chain because your supply chain is now reliable. Most importantly of all, you’ve now got a safe plant because everything’s in control and people aren’t running around.
The challenge of culture change
It’s hard to get there. All of that requires a cultural change in your organisation, rewarding the people who sit around in control rather than rewarding the heroes the leap in and solve the problem when it fails.
You’ve got to think about your change journey. It’s about creating the urgency for change, creating the situation where people recognise that the status quo is not a tenable position and we’ve got to change. To do that, we need data again – the data that demonstrates the status quo is not a tenable position.
Refresco are a contract beverage packer and on a big rotary can filler, we put a vibration monitor on the main gearbox. What we saw shortly after installing it was a catastrophic failure of their lubrication system, so these big rotary bearings are out three metres and it’s horrifically expensive to change them.
What they’d done is put the wrong lubricant into the automatic lubrication system and by mixing two lubricants, they effectively frozen the lubricant and then we’re getting no oil delivered to the bearing. A very dramatic increase in lubrication allowed them to limp through to the end of that production run, so they got through without interrupting the customer and impacting the supply chain. They scheduled in a flush through and clean of the lubrication system, then changed the grease nipples to ensure that you couldn’t put the wrong lubricant in again.
In this case, it was like a £100,000 saving. The culture change led them to expand that fixed condition monitoring to other lines to see the benefit elsewhere.
Change thinking first
A final word from one of the greats of the world of maintenance, John Mabry… Maintenance problems are best solved in two stages. First of all, change the way people think. Secondly, apply their changed thought processes to technical and process problems, one step at a time. Still just as fresh today as it was 28 years ago when he wrote this.