Is Digital Transformation a Myth?
4 min read
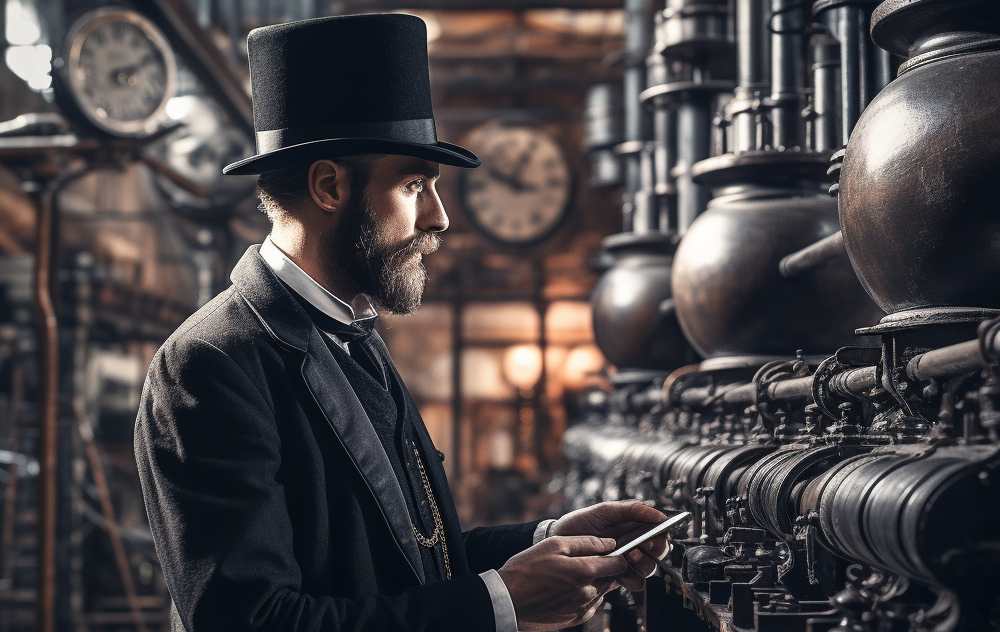
We investigate how extensively maintenance engineers are (or aren't) adopting and utilising digital technologies.
“When we asked them about digital transformation, only a minority said that’s what is in their plan” observed Emma Botfield, RS Managing Director, UK and Ireland, in her foreword to Industry in Motion: Maintenance Engineering Report 2023.
The report, produced by RS and the Institution of Mechanical Engineers (IMechE), offers fascinating insights into perceptions of digital technology within the maintenance engineering industry. Here we explore its findings and ask, despite the hype surrounding concepts such as Industry 4.0 and the Industrial Internet of Things (IIoT), is digital transformation a myth?
Read on to find out.
A mixed picture
As Botfield’s comment indicates, the survey of IMechE members that provides the foundation for Industry in Motion seems to suggest that few in the industry are actively engaging with digital technologies. When asked directly “Is your company planning a digital transformation of your maintenance assets and facilities?”, just 18% answered yes – and 82% answered no.
Only 16% of respondents reported using IIoT
Other similar statistics emerged from the survey too. Only 16% of respondents reported using IIoT, for instance. When it comes to monitoring and managing maintenance, although 49% mentioned Computerised Maintenance Management Systems (CMMS) and 39% Enterprise Asset Management (EAM), more said Excel spreadsheets (51%). Around a third even said paper records.
Some of this is down to shortcomings with the technology rather than industry resistance, argues Richard Jeffers, Managing Director of plug-and-play IIoT platform RS Industria. “I don’t think that’s a maintenance problem,” he explains. “I think it’s indicative of poor integration between different technology platforms and the fact that the Microsoft desktop suite is designed to be super-easy to manipulate data.
“There are not many people out there who have nothing but Excel”
Richard Jeffers, Managing Director, RS Industria
“Quite often the fastest and cheapest way to manipulate data into reports is to use Excel,” he continues. “There’s a difference between using Excel for reporting and forecasting – which I would suspect a lot of people do – and using Excel to manage the maintenance workflow, which I doubt many really do.
“There’s an awful lot of CMMS platforms out there at a variety of price points and it’s rare to come across a factory that has no CMMS platform. There are not many people out there who have nothing but Excel.”
Questions around terminology
It is also important to consider the language used when asking about digital transformation, says Jeffers. He offers an anecdote to illustrate why. “A customer told me they had a policy of not using the Cloud,” he recalls. “I said, do you use Office365? They said yes – well that’s on the Cloud.
“If you ask people if they collect data from their machines and use that to make decisions, a lot more would say yes.”
“IIoT, digital transformation and Industry 4.0 are… not shop floor buzzwords”
Richard Jeffers, Managing Director, RS Industria
Differences in terminology can cause confusion and even obscure the extent to which maintenance engineers are utilising digital technologies. According to Jeffers, “IIoT, digital transformation and Industry 4.0 are terms the average operational maintenance person doesn’t use. They’re not shop floor buzzwords.
“People talk about these new developments like they’re a revolution, when in fact it’s an evolution, because there’s a lot of good automation in factories and there has been for a long time.”
Further analysis of the RS and IMechE survey supports this claim. While only 16% of respondents said they use IIoT, for instance, many more reported deploying condition monitoring techniques that rely upon digital technologies including vibration analysis (44%) and current monitoring (43%).
This is in part thanks to lower prices making condition monitoring devices more accessible.
“The cost has plummeted,” says Jeffers, “and we are able to apply better data science to analyse what monitoring is telling us.”
Recognition of advantages
The survey also shows that maintenance engineers do recognise the benefits that digital transformation offers. A third of respondents, for example, plan to use preventative maintenance strategies, which rely heavily on digital technologies, to reduce downtime.
Asked about the benefits of condition monitoring, 68% said it improved their understanding of the health of an asset, 53% said they were better able to predict failure and 27% said it changed the behaviour of employees in the way they managed assets.
Not every organisation is, however, equally well placed to take advantage of digital technologies. “All the condition monitoring and data science in the world won’t help you if your culture is one of being reactive and firefighting,” warns Jeffers.
“Businesses that are trapped in a reactive cycle are not going to benefit”
Richard Jeffers, Managing Director, RS Industria
“The businesses that are doing well out of new tech are the ones that were doing well anyway, because they’ve got the right management processes. Businesses that are trapped in a reactive cycle are not going to benefit because they don’t have the right mindset and ways of working.”
Seeking support
Some barriers to the successful implementation of digital technologies can be overcome with input from trusted suppliers. Outsourcing offers a vital source of support, especially if the in-house maintenance team lacks the necessary expertise or capacity. Among survey respondents, half were considering outsourcing predictive maintenance technology and just over a third energy loss surveys. Why? 57% turned to outsourcing because too many specialised skills were required. Forty percent said staff didn’t have the skills and 35% mentioned reduced headcount as a factor.
Advantages include cost effectiveness
There are also positive reasons for choosing to outsource aspects of digital maintenance. Those who completed the RS and IMechE survey said advantages include cost effectiveness (32%), flexibility (32%), overall efficiency (28%), reduced probability of failure (26%) and decreased downtime (26%).
It is clear, therefore, that maintenance engineers are using a range of digital technologies to help them measure, monitor and manage assets and bringing in external providers for what they cannot do themselves. As a profession, they are certainly engaging with digital transformation – even if that is not the label that they use to describe it.
Learn more about how the industry is changing by downloading the full Industry in Motion: Maintenance Engineering Report 2023.