Case Study: Early Warning Saves High Speed Filling Line at Refresco
2 min read
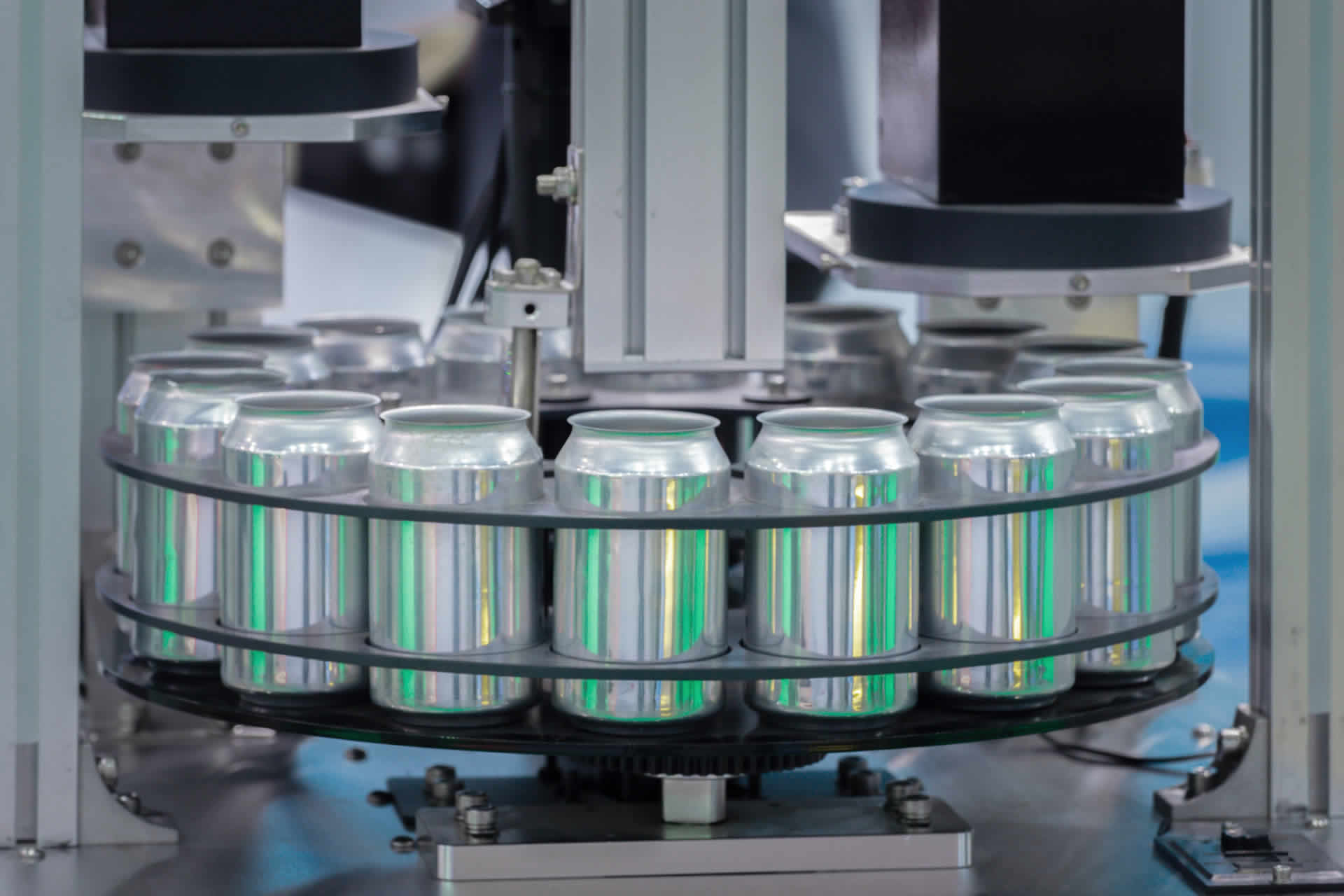
Discover how RS Industria’s manufacturing improvement service helped Refresco’s Pontefract plant to predict and prevent failure on a critical high-speed filler, thanks to continuous vibration monitoring.
The Challenge
To say that a bottling plant is fast paced is something of an understatement.
High-speed beverage packaging lines are extremely complex assets that whizz bottles and cans around in a blur, with the heart of the operation often being the high-speed filler. This complex rotating asset is vital to the operation, with any downtime causing huge upheaval in terms of both repair costs and significant disruption in product supply.
This is something the Refresco Group is all too aware of. As the world’s largest independent bottler with production sites worldwide (including six in the UK), it produces over 30 million litres of popular branded and private label drinks every day, with a huge range of bottles, cans, cartons and cuplets.
Refresco’s Bondgate site in Pontefract recently assumed operational responsibility for a new high-speed can filler and seamer – a Krones Can Filler TK 3600. At 1,500 cans per minute, this unit is one of the most utilised fillers in the plant, so it’s crucial that it remains in operation without any failures.
With the filler’s 12-month service package drawing to an end, Refresco would now be solely responsible for the ongoing maintenance of this critical asset. This is a huge responsibility.
If the main ring bearing was to fail, for example, the downtime would lead to significant upheaval and cost; not least because these bearings are typically manufactured to order and could take months to replace.
The Solution
Having already seen benefits from using periodic vibration analysis on some of its critical high-speed fillers, Refresco decided to extend this solution to the new filler, and use fixed vibration sensors to provide continuous vibration monitoring.
This service would be provided by RS Industria’s asset monitoring platform, with the resulting operating data used not only to understand ongoing wear of the filler, but also protect it against unexpected failure.
The Journey
Drawing on its extensive manufacturing experience and deep knowledge of operational technology (OT) automation, the RS Industria team identified the correct monitoring solution to ensure that all main failure modes were detected, despite the relatively low rotational speed.
In total, 14 individual accelerometers were used to cover the main rotating components of the filler. These were all linked to Siemens vibration monitoring cards, which were then directly connected to RS Industria’s onsite Edge Gateway.
Data flowing from these various sensors were integrated into a single point of insight, providing a total view of the filler.
Using this customised RS Industria dashboard, Refresco’s maintenance team were now able to easily view real-time vibration data from each sensor. Having created vibration baselines that consider the different speeds of the filler when various products are running, the system can trigger ‘context sensitive’ alerts when normal vibration levels are exceeded.
The Outcome
Within a few weeks of its initial operation, the RS Industria platform had already detected abnormal vibration levels on the main ring bearing.
The system discovered that this was due to the bearing being starved of lubrication, caused by a blocked grease line. Continued running would have irreparably damaged the bearing, resulting in downtime and a costly replacement. The total cost of parts and labour of such a bearing failure can be in the region of £100,000, not including the loss of product capacity during that period.
Rather than using intermittent monitoring or inspection, Refresco now relies on continuous vibration monitoring delivered by RS Industria. This has enabled it to move to a planned and predictive maintenance culture, rather than reactive.
Simple, fast, and affordable to deploy, RS Industria offers a solution where the cost of monitoring is a tiny fraction of the price of unexpected failure.
“The whole process was easy,” says Karl Hewes, Control Systems Engineer at Refresco Bondgate. “At the initial meeting with the Industria design team, we talked through the information we’d like to see and where we’d like to see it. They showed us what they could offer, and we went for it.”
RS Industria gives you the power run a reliable, efficient, and eco-conscious production line, reducing production losses through the measurement and optimisation of…
Ready to learn more?
Read on to ‘Balancing OT & IT’.