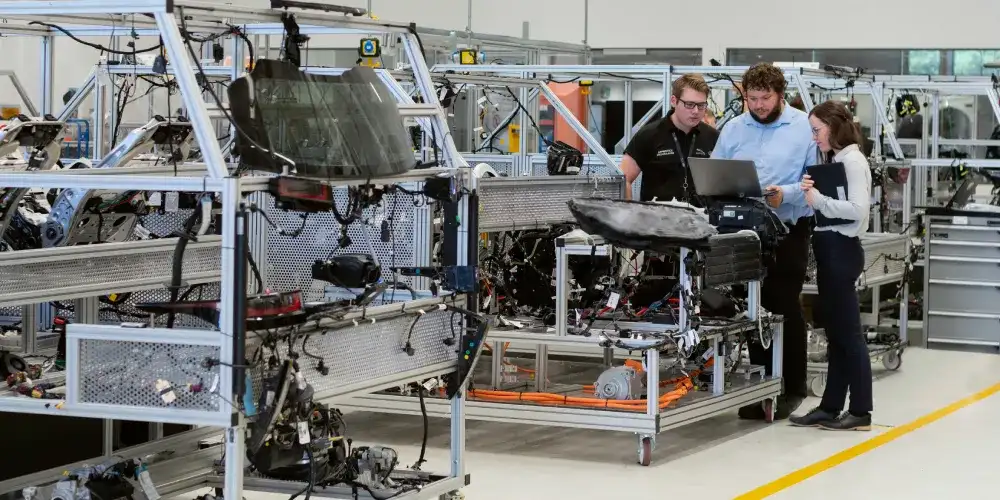
Start your Industry 4.0 journey with Industrial Internet of Things (IIoT) technologies that help maintenance engineers to work more efficiently and a smart factory will follow
The Industrial Internet of Things (IIoT) is “the digital backbone” of manufacturing transformation, says professional services giant PwC, and using devices connected to the internet to monitor asset performance is the first step in creating a smart factory.
Manufacturers are installing more and more devices such as sensors to harvest operational data from machinery, reinforcing the important role that IIoT plays in Industry 4.0. That said, “Industry 4.0 is more than just plugging a sensor on your rotating bearing and monitoring it in the cloud,” argues Ian Clarke, CEO of future technology consultancy Velocumen.
“It’s about being able to take that data and using it to influence what you’re doing across the factory as part of a holistic solution.”
A smart factory game changer
One area where the smart factory data that you can access via IIoT makes a big difference is maintenance engineering.
Rather than traditional approaches based on time or utilisation, digital data provides insights into how equipment is performing in real time, allowing for more effective and efficient maintenance – and the development of leaner processes.
“Condition monitoring is as simple as giving you an extra piece of information,” explains Gary Harvey, Head of Field Services at RS UK & Ireland. “You can then use that information to help make a decision about when you do maintenance at a time convenient to you.”
“We can now gather huge volumes of data…and that’s a real game changer”
Dr Moray Kidd, maintenance engineering academic
Dr Moray Kidd, a maintenance engineering academic, also emphasises the importance of analysing data rather than simply collecting it. “We can now gather huge volumes of data that can often directly or indirectly infer the condition of industrial machines and that’s a real game changer,” he says.
“Some companies are sat back gathering large volumes of data, even using machine learning. But they’re not acting on that data and they won’t see a difference in operational performance.”
The challenge for SMEs
Despite the benefits that it offers, if your organisation has yet to make the most of IIoT, you’re not unusual. A global survey by PwC discovered that just 3% of manufacturers believe they have a fully digital factory, while two-thirds of those surveyed said they were still at the start of the digital transformation journey.
It’s a process that involves an assessment of your organisation and staff skill levels as well as an investment of time and money, which the PwC study acknowledges is challenging for companies large and small.
“They haven’t really got a plan to move them from where they are now to where they’d like to be”
Gary Harvey, Head of Field Services, RS UK & Ireland
However, small and medium enterprises (SMEs) particularly struggle with digitalisation. “They haven’t really got a plan to move them from where they are now to where they’d like to be,” states Harvey, “which is usually to be in more control than they are today.”
Clarke also believes that lack of planning holds smaller companies back. “In almost every business I visit, not all of the machines are connected into a site-wide digital strategy,” he says. “Many companies struggle to create a sensible strategy for how they’re going to find out what is going on in those machines.
“In the very biggest companies, of course, it’s happening. But the vast majority of British manufacturing and process industries fall into the category of SMEs and they’re totally under-connected when it comes to a site-wide digital strategy.
“I see them every week. They might have spent half a million pounds on a machine but if they want to find out what’s going on with it, they have to walk up to it or speak to the machine operator who gives them a piece of paper with the batch records.”
Begin with legacy equipment
“You don’t need to go out and buy all new kit”
Ian Clarke, CEO, Velocumen
Whatever machinery your organisation already has, it can provide the starting point for your IIoT journey. “The vast majority of machines in factories are old – in many cases they’re over 40 years old,” notes Clarke, “but you don’t need to go out and buy all new kit to start your digital journey.”
Liaise with original equipment manufacturers (OEMs) to check that you can connect their machine to your Industry 4.0 system and access the data that it generates. Then, as Clarke points out, condition monitoring devices can be added to almost any machine. These can, for example, detect excessive vibration. Pair this with oil analysis and you’ll see failure warning signs far earlier.
Start small then scale
Going further, you can begin to create a smart factory by building up a comprehensive view of how the whole facility is operating.
How? By bringing together all the data gathered by condition monitoring devices and Programmable Logic Controllers (PLCs). PLCs are industrial computers and they control how an asset works. Using sensors and actuators, they ensure that the system performs a particular function.
Experts at the Manufacturing Technology Centre (MTC), which has created smart factory use cases as part of its mission to help UK businesses overcome the hurdles that prevent the adoption of IIoT and Industry 4.0 more broadly, offer useful advice.
“We’re trying to demonstrate what we call the art of the possible,” says Naim Kapadia, MTC Electronics Technology Manager. “That’s what we’re about. We are trying to demonstrate it in a factory so that people can see it and say, ‘This could be possible for us to do.’”
“Trying to tackle too much too soon will slow you down”
Naim Kapadia, Electronics Technology Manager, MTC
Although digital transformation will give your business a competitive advantage, Kapadia urges organisations to introduce changes gradually. “Think big, start small and scale fast,” he advises. “Trying to tackle too much too soon will slow you down and make it harder to implement.”
“My recommendation is start with a specific use case,” he adds. “Stay focused on the why and continue to apply the lessons learned. It’s a key starting point to justify investment so you’re not asking for millions of pounds to start the ball rolling.”