Seven ways RS Industria saved a leading food manufacturer time & money
2 min read
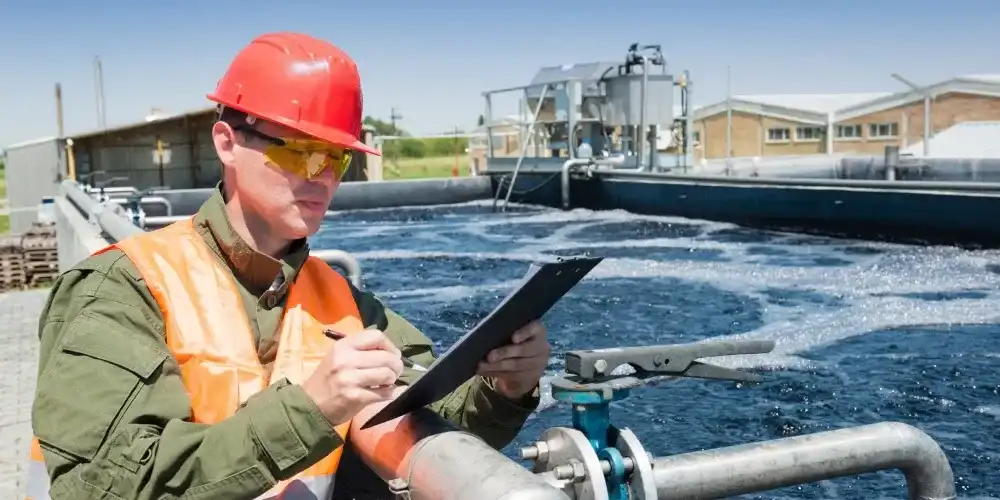
Food and taste leaders, Kerry Group, are passionate about their products. Now a global entity, Kerry started life as a small dairy company in Ireland. 50 years on, the business has undergone major change, innovation, and transformation to become a global manufacturer, producing everything from functional and nutritious ingredients to food and beverage solutions.
Kerry‘s innovative and high-growth mindset extends to its operations, where engineers are encouraged to reduce downtime by delivering best-practice solutions and continuous improvement.
The Worcestershire-based Tenbury Wells site is a key part of Kerry’s UK footprint, producing sweet and fruit ingredients such as preserves, fillings, and sauces.
Local to the site are waterways that need to be kept free of pollution, so engineers working on the site’s wastewater plant need to continually monitor levels to maintain environmental compliance.
Single overview of condition monitoring
The ageing wastewater plant had been expanded over the years to match the growing needs of the Tenbury site. Necessary daily manual readings took time as tanks were located in remote locations, while the complex nature of the plant made it difficult for engineers to have a single overview of compliance and condition monitoring.
So how did the modular Industrial Internet of Things (IIoT) platform, RS Industria, help and what were the results?
RS Industria digitally connected the site’s complicated network of pumps, valves, meters, and gauges, replacing time-consuming manual activities and giving greater visibility to site engineers.
Limits were set for the key parameters necessary for effluent control such as COD and pH. If these were approached, engineers at the site would receive text alerts so they could act quickly and resolve the issue.
Within weeks of its implementation, data insights from RS Industria meant Kerry’s engineers could efficiently achieve the required level of environmental compliance and better understand their water usage, saving 100,000 litres/day in the process.
Detailed and valuable insight
Thanks to the delivery of detailed and valuable insight, RS Industria has changed the way the plant performs by:
- Enabling targeted improvement activity to reduce wastewater COD and freshwater consumption within weeks.
- Removing the need for time-consuming manual daily meter readings in remote locations.
- Automating essential measurements necessary for environmental compliance, with pH control improved, total COD reduced, and many people hours saved.
- Providing a ‘Compliance Dashboard’ for greater visibility on effluent quality and daily plant performance, allowing the team to check key wastewater parameters and tank levels in real-time.
- Creating detailed records which can be used to demonstrate compliance history to relevant authorities.
- Giving early and timely warning alerts, enabling rapid, corrective action.
- Improved productivity, with the team now able to focus on maintaining core production processes with fewer interruptions, resulting in improved production uptime.
With a reduction in effluent disposal costs - as the volume discharged is now much lower - and major water savings as a direct result of better effluent treatment control – RS Industria is making a difference daily for Kerry’s engineers.
Interested to know how our user-friendly system can make a difference to your business?