Compressors
Most industrial refrigeration compressors are large, mechanical units that form the heart of industrial cooling and heating. They draw refrigerant from the evaporator at a relatively low pressure, compress it and then discharge it to a condenser where it is cooled.
The refrigerant then moves to the expansion valve and the evaporator – where it absorbs heat as it changes physical state - before being compressed again.
There are different types of compression mechanisms that are typically used in factory environments: reciprocating (piston), rotary (vane) and screw compressors (three different types).
The refrigeration compressors typically cool a glycol-water mixture or brine contained within a closed thermal exchange system, which is then used as a secondary coolant and pumped as required to chill or freeze environments or equipment, enabling producers to lower the temperature of a product dramatically over a short period of time.
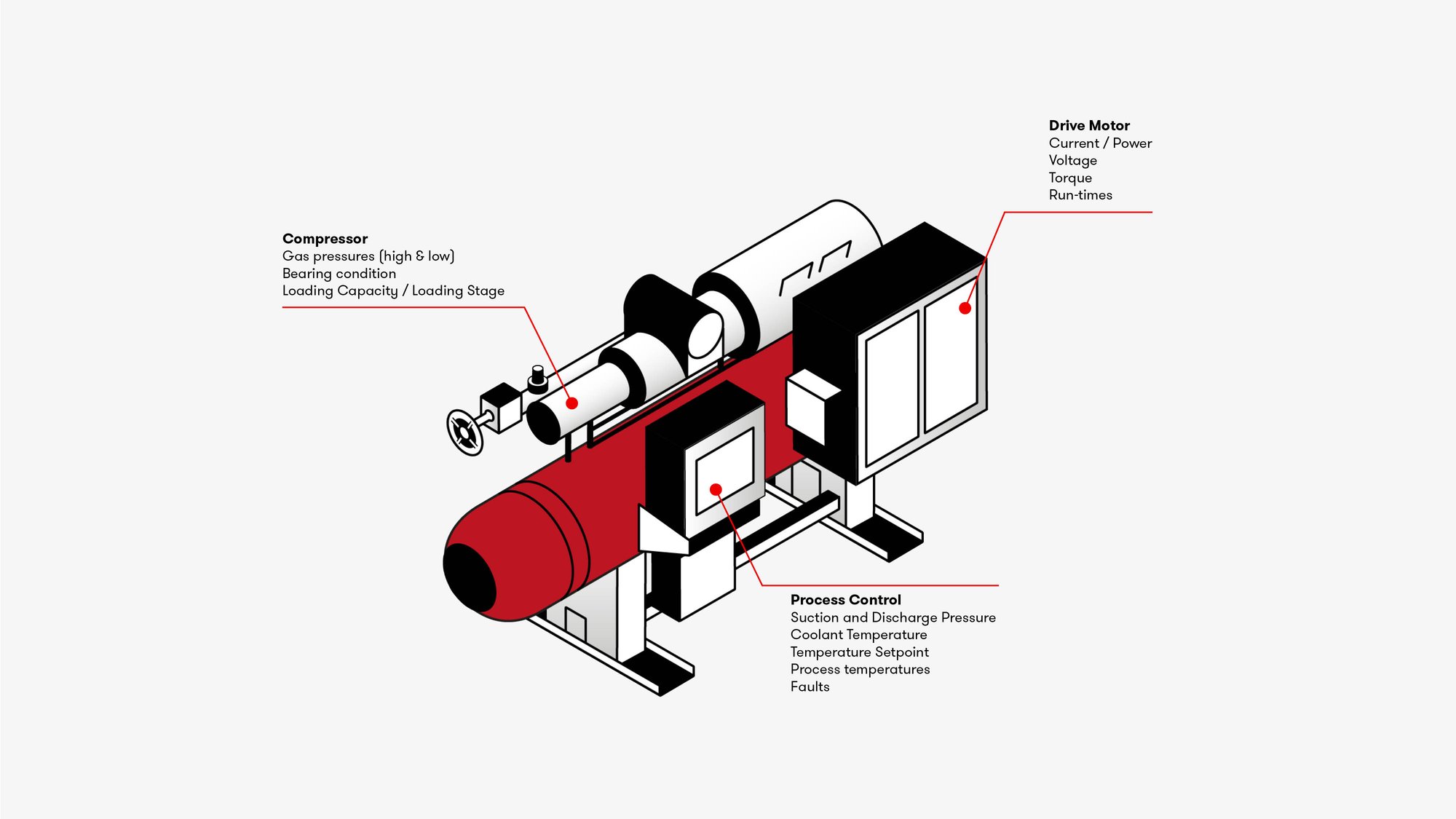
Potential Savings using RS Industria.
£0
Potential Savings in Energy Costs
Overview
Compressors are important tools in food and beverage production. From compressing air in pneumatic systems (such as conveyor belts) to cooling refrigerants, compressors work by condensing air or refrigerant gases and then releasing them at a higher pressure.
They are highly versatile and, as a result, often used for a range of applications on a production line. With RS Industria, you can unlock the dormant data held in your compressors, allowing you to leverage all-new insights to improve operational performance, reliability and sustainability.
Energy Consumption
The Challenges
The compressor is the heart of a refrigeration unit compressing the refrigerant through mechanical compression. Successful operation of the compressor is a key factor in achieving an efficient industrial cooling application.
There are several methods of modulating cooling capacity, depending on the compressor type. Reciprocating compressors are start/stop, variable-speed screw compressors use pressure control valves and fixed-speed screw compressors use a slide valve. These various modes of operation can make it difficult to accurately calculate energy consumption.
Our Solution
Energy data often be collected direct from the variable speed drive, when used to drive the compressor. If no electrical consumption data is available, then energy meters / current transformers can be easily installed which can pass data directly to RS Industria.
Book an Energy Consultation to find out how much you could save!
Your Benefits
The energy consumption per compressor can now be accurately measured, highlighting any over-operation and enabling the overall refrigeration system’s efficiency to be calculated.
Using this information, it should be possible to optimise the system. For example, a 45kw Screw Air Compressor running for 12hrs per day @ 50p/kWh, will cost £98,550 per annum to run (@ June 2022 prices).
A 10% reduction in consumption due to optimisation will save nearly £10,000 every year.
£10,000 Energy Annual Saving
Operations
The Challenges
- These assets are often process critical
- Loss of refrigeration capacity can cause huge disruption to manufacturing
- Raw materials are often wasted as a result of cooling loss
- Regulatory and compliance issues can arise when correct operating temperatures are not maintained
- Health and Safety issues can arise if correct controls are not in place, especially if ammonia or CO2 is uses as a refrigerant. This can also pose an environmental risk
Our Solution
Process data such as chiller temperature can often be captured directly from the PLC or control system. This will aid accurate operational recording as well as improving problem solving. Where PLCs are not used, a separate data collection unit can be fitted to mirror existing control signals.
Data such as stop/start timings, freezer door opening events and their duration, all create visibility of the system’s operational cycle.
Your Benefits
Continuous monitoring of the refrigeration system enables:
- Detection of liquid slugging
- Visibility of coolant operating temperatures and pressures
- More efficient operation •Detailed temperature history for regulatory and compliance audits.
- Greater understanding of the operating cycle of the compressors and overall cooling system
- Optimisation of the whole cooling cycle
Maintenance
The Challenges
Cooling circuit changes can result in a capacity mismatch between the compressor and evaporator, leading to excessive loading
- A poorly sized or malfunctioning thermostatic expansion valve and high oil temperatures can all lead to premature failure of the refrigeration compressor
- Slugging is a condition where a liquid (oil or liquid refrigerant) enters the compressor and causes damage (usually on startup)
- Other common causes of early failure are dirty evaporators, dirty filters, dirty condensers - all of which will increase the compressor workload.
Our Solution
Much of the energy data collected can also be used as leading indicators of failure. By tracking current/power consumption, changes in the electrical load can be used to indicate changes in the cooling system. Using the additional data from process control parameters, a more complete picture of asset reliability can be created.
Additional protection of the compressor motor and bearings can be added using a vibration sensor, thus monitoring other mechanical stresses such as looseness & misalignment of the compression elements (pistons or rotary vanes for example) bearing wear or lubrication failure on contact surfaces
Your Benefits
- Reduce the risk of unplanned failure, avoiding secondary damage and reducing MRO spend
- Enable the move from reactive to planned maintenance
- Vibration data can highlight over or under lubrication of key components
- Protect mechanical assets such as compressors using multiple vibration bands, combined with ‘smart’ early-warning alerts


Improve Safety

Increase Efficiency
An Early Warning System for Your Factory
Find out how we can help lower energy usage, enhance reliability and improve operational performance: in a way that is simple, fast and affordable.
Book a Demo