Conveyors
Pack Conveyors offer full automation options for moving products through each stage of the production process.
The products can be packaged in either their primary container or their secondary distribution packaging and automation minimizes product handling, limiting the risk of damage and handling errors. Pack Conveyors are extensively used in consumer product manufacturing, from bottling plants to frozen food.
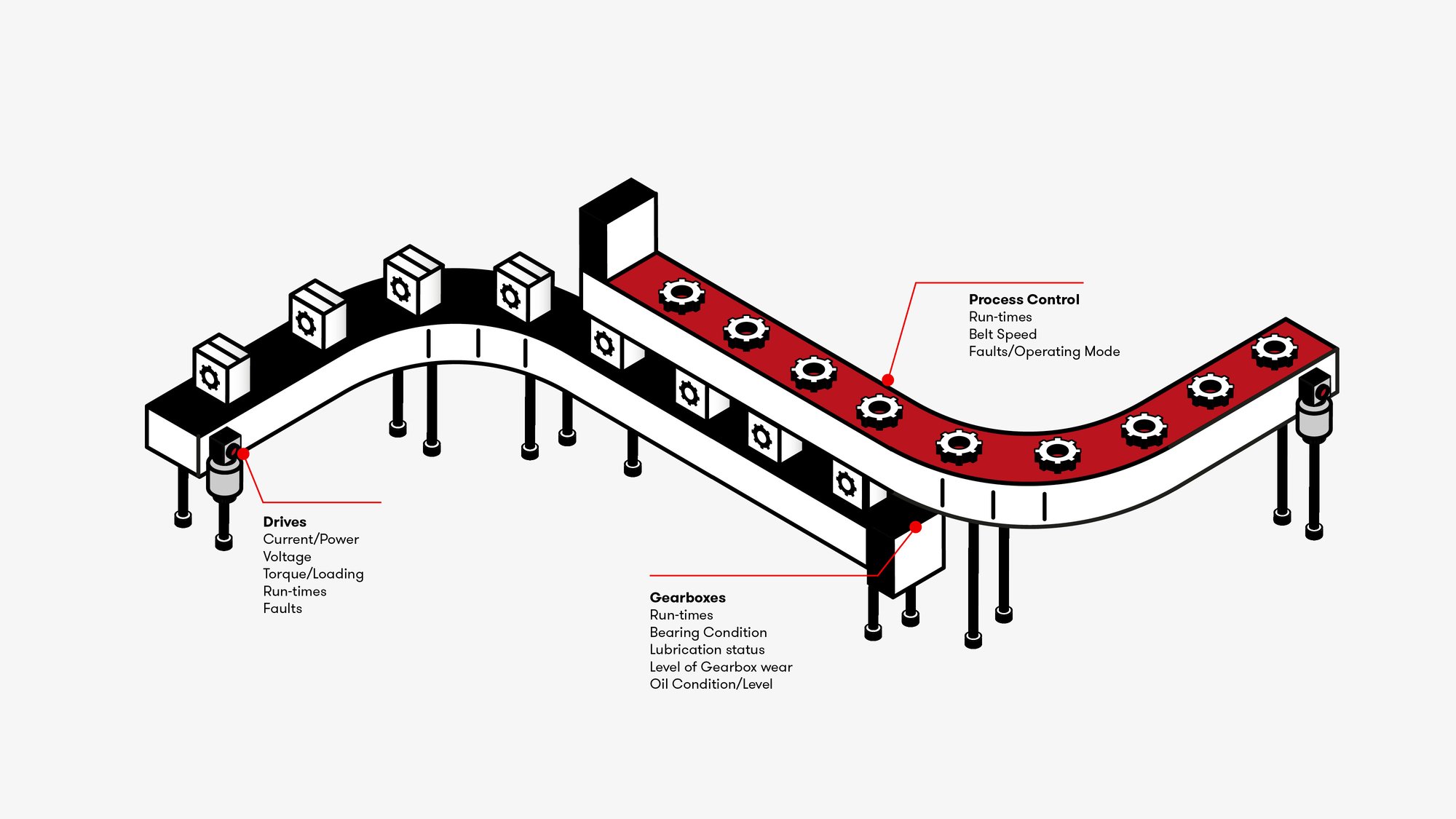
Potential Savings using RS Industria.
£0
Potential Savings in Energy Costs
£0
Reduction in Maintenance Costs
£0
Reduction in Operation Costs
Overview
Conveyors allow for efficient and automated movement of products throughout the food and beverage manufacturing process.
By integrating with other equipment - such as filling and packaging machines – conveyors help to increase production rates and reduce labour costs, while simultaneously shrinking the risk of human error.
RS Industria is the simple, fast and affordable way to enhance reliability and uplift the operational performance of your conveyors – all while helping you to meet your sustainability objectives.
Energy Consumption
The Challenges
Depending on their application, conveyor systems can form a significant portion of the energy consumption of any given line.
Where the health of the asset is not optimal, wasted energy usage can go unnoticed. Potential efficiency savings of the line are missed where the energy data has insufficient granularity to highlight potential problems with sub-components, such as drives or gearboxes.
Conveyors can run continuously even when empty, if there is no product detection system in place, thus wasting energy.
Inability to quantify the energy consumption changes when accumulation conveyors fill to capacity.
Our Solution
Energy data can often be collected direct from the variable speed drive, when used. If no electrical consumption data is available, then energy meters or current transformers can be easily installed which can pass data directly to RS Industria.
Book an Energy Consultation to find out how much you could save!
Your Benefits
The energy cost for a given conveyor can be quantified. The ability to also highlight wasted energy from over-operation (running at higher speeds & accelerations than might be necessary, or running empty).
£5,500 Energy Annual Saving
Operations
The Challenges
Packing conveyors are at the heart of a process line, moving component parts or finished products along the line, and when faulty they impact the entire manufacturing line. Most conveyors are single line without bypass lanes.
Repairs can be complex resulting in additional delays.
Conveyor assets often need to be optimized in terms of speed and acceleration to maximise productivity.
Our Solution
Process data such as line speeds, acceleration & deceleration rates can often be captured directly from the PLC or control system. This will enable accurate operational recording as well as aid problem solving.
Your Benefits
Maximise line speed and acceleration rates for most efficient operation of the whole line.
Minimise the losses as a result of conveyor system failure.
Prolong the lifespan of component parts, by ensuring they are operating within their correct system parameters, such as loads, speeds, belt tensions etc.
£6,000 Operation Annual Saving
Maintenance
The Challenges
Bearing failure can result from mechanical issues such as looseness, misalignment and imbalance, negatively impacting asset life.
Conveyor belts can be overtensioned or fitted with the wrong specification belt, resulting in excessive loading on the motors and gearboxes.
The drive for ever-improved throughput of the conveyor system can result in programmed speeds and acceleration rates exceeding design specifications, which can cause damage to the line and result in early component failure.
Our Solution
Monitoring current & torque can detect changes in the loading of the pack conveyor. Vibration and temperature sensors on the motors, gearboxes and bearings can be used to monitor specific leading indicators of failure.
Capturing process control system data, such as running speed, stops, faults and operating modes, provides accurate operational recording and improves problem solving.
Oil condition sampling, either online or periodic, can give a very early indication of potential failures and highlight operations that may cause excessive degradation of the mechanical components.
Your Benefits
Much of the energy data collected can also be used as leading indicators of failure. Through tracking current and torque, changes in the electrical load can be used to indicate changes in the system being driven. This can yield early detection of belt quality or over-tensioning issues with the conveyor. Using the additional process parameters, we can build a picture of how the asset performs from a reliability standpoint.
Additional protection of the motor, gearbox and bearings offered by vibration sensors allows monitoring of mechanical stresses such as looseness, misalignment, bearing failure & gearbox degradation.
£2,000 Maintenance Annual Saving


Increase Efficiency

Save Costs
An Early Warning System for Your Factory
Find out how we can help lower energy usage, enhance reliability and improve operational performance: in a way that is simple, fast and affordable.
Book A Demo