Mixers & Homogenisers
Industrial homogenisers and mixers are used across a range of different sectors from bakeries through to the preparation of lubricants. They can be designed to mix a range of products across all three phases and can be both batch and inline.
High speed batch mixers are used in a range of different applications such as bakeries and in the production of potato snack, crackers, hard biscuits, rotary, wire cut and pet food biscuit dough with mixing capacities up to several tonnes in capacity. They can be either vertical or horizontal shaft arrangements and are fitted with a variety of systems to handle the feedstock and the finished mix.
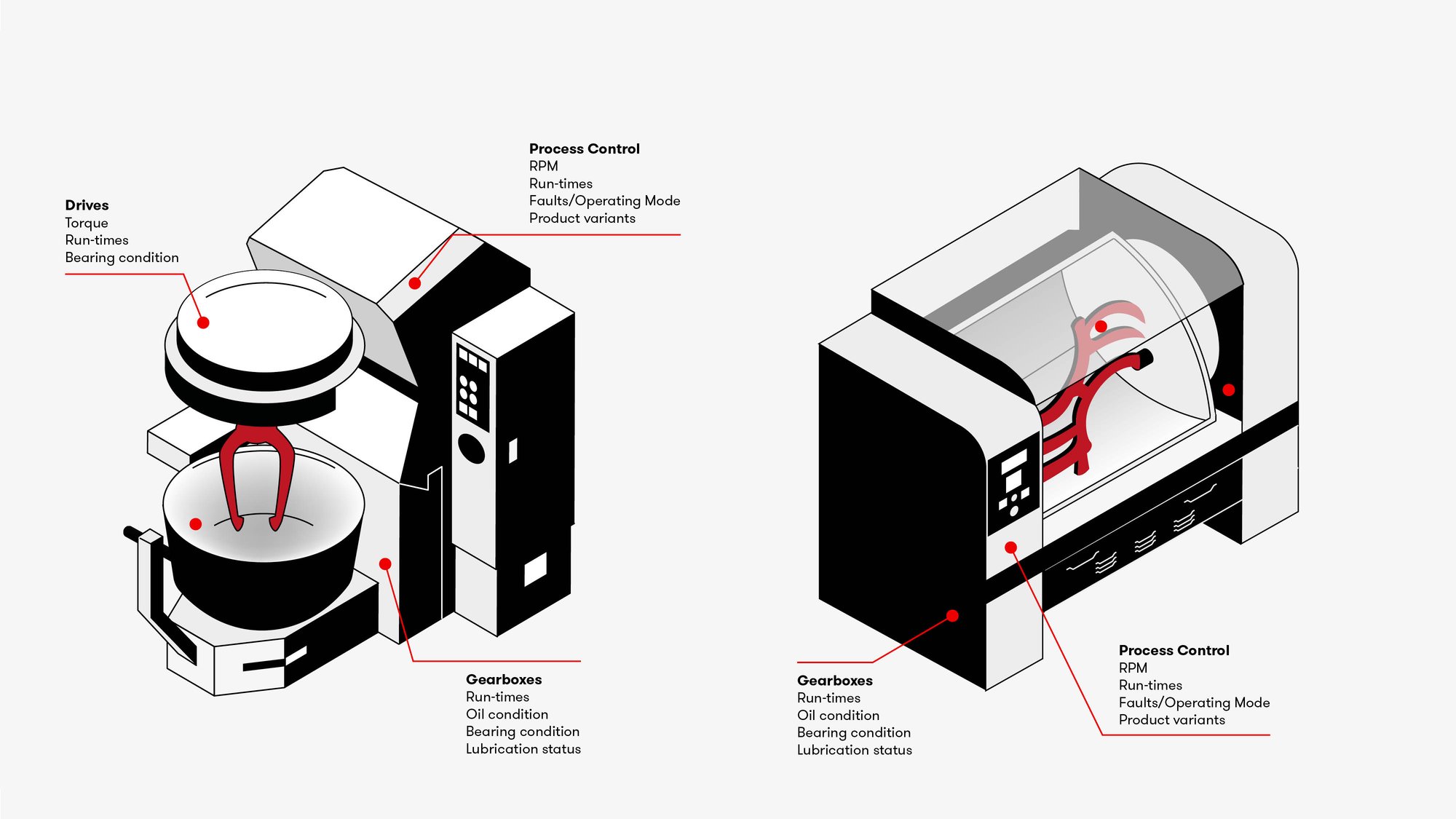
Potential Savings using RS Industria.
£0
Potential Savings in Energy Costs
£0
Reduction in Downtime Costs
£0
Av. Cost of Scrapping a Tonne of Batter
Overview
Mixers and homogenisers are crucial tools in food and beverage production, ensuring the consistency, quality, and safety of your final product.
By allowing you to measure and optimise asset performance, RS Industria will help to guarantee the high standards you rely on – quickly, simply, and affordably.
Energy Consumption
The Challenges
Mixers tend to be large, but intermittent, power users, with a soft start. It can be difficult to see how energy consumption is changing over time, leading to potential energy losses going unnoticed.
Our Solution
Energy data often be collected direct from the soft start of inverter drive, when used. If no electrical consumption data is available, then energy meters can be easily installed which can pass data direct to RS Industria.
Book an Energy Consultation to find out how much you could save!
Your Benefits
A 300 kW mixer will consume around £200,000 worth of electricity (June 2022 prices). Unresolved mechanical issues with motors can drop the efficiency of the motor by 10%, increasing electricity cost by £20,000 per annum.
£20,000 Energy Annual Saving
Operations
The Challenges
Accurately tracking the run time of mixers can be key to the quality of the mixed products. On older systems this can be challenging, relying on operators to manually start and stop the mixers and record the mixing times. Where quality issues do arrive, it can be hard to accurately track back to the actual operating conditions, making problem solving extremely difficult.
Our Solution
Process data such as running speed, stop, fault and operating mode can often be captured directly from the PLC or control system. This will aid accurate operational recording as well as aid problem solving. Often other setup and operating parameters can also be captured, further enhancing the ability to problem solve production issues. Where PLCs are not used, a separate data collection unit can be fitted to mirror existing control signals.
Your Benefits
Better understanding of quality issues during mixing could avoid the scrapping of a batch of batter in excess of £3,000 per tonne. Saving just two batches of batter in year 1 would pay for the set-up and monitoring costs.
£6,000 Operation Annual Saving
Maintenance
The Challenges
Mixers and homogenisers have high, but intermittent, loads on the moving parts, particularly on start up.
Bearings can fail due to over tension of drive belts and wash out of lubricant, lubrication systems can be blocked, shafts can be bent out of true and gearboxes can suffer from water ingress. All of these will dramatically shorten the life of the asset whilst in service failures can lead the the need to waste the current batch, with a high cost in terms of wasted ingredients.
Our Solution
Much of the energy data collected can also be used as leading indicators of failure. Through tracking current and torque, changes in the electrical load can be used to indicate changes in the mechanical system being drive.
Where more granularity on the potential failure is required, perhaps to increase the warming time, we would look to use vibration and temperature sensors on the motor, gearbox and shaft with the sensor choice driven by the application. This would provide real-time data on the assets and pickup leading indicators of failure.
Your Benefits
Preventing a catastrophic breakdown will avoid spares spend and production downtime. A typical breakdown would be 12 hours lost time at £1,000 per hour, resulting in a £12,000 cost.
£12,000 Maintenance Annual Saving


Solve Problems Faster

Optimise Energy Usage

Single Point of Insight
Improve Operational Performance Now
Find out how we can help lower energy usage, enhance reliability and improve operational performance: in a way that is simple, fast and affordable.
Book A Demo