Fire Tube Boilers
Fire Tube Steam Boilers are the most common technique for the production of saturated steam, high pressure hot water or superheated steam in industrial settings. Steam is generated by heating water in a pressurised drum by means of hot gases, which are produced from the combustion of liquid or gaseous fuels circulating through submerged tubes.
The large volume of pressurised stored water is used to resolve the standard potential variables that affect all boiler type systems, including variations in the feed water, fuel, combustion quality, temperatures and, importantly, steam load variation.
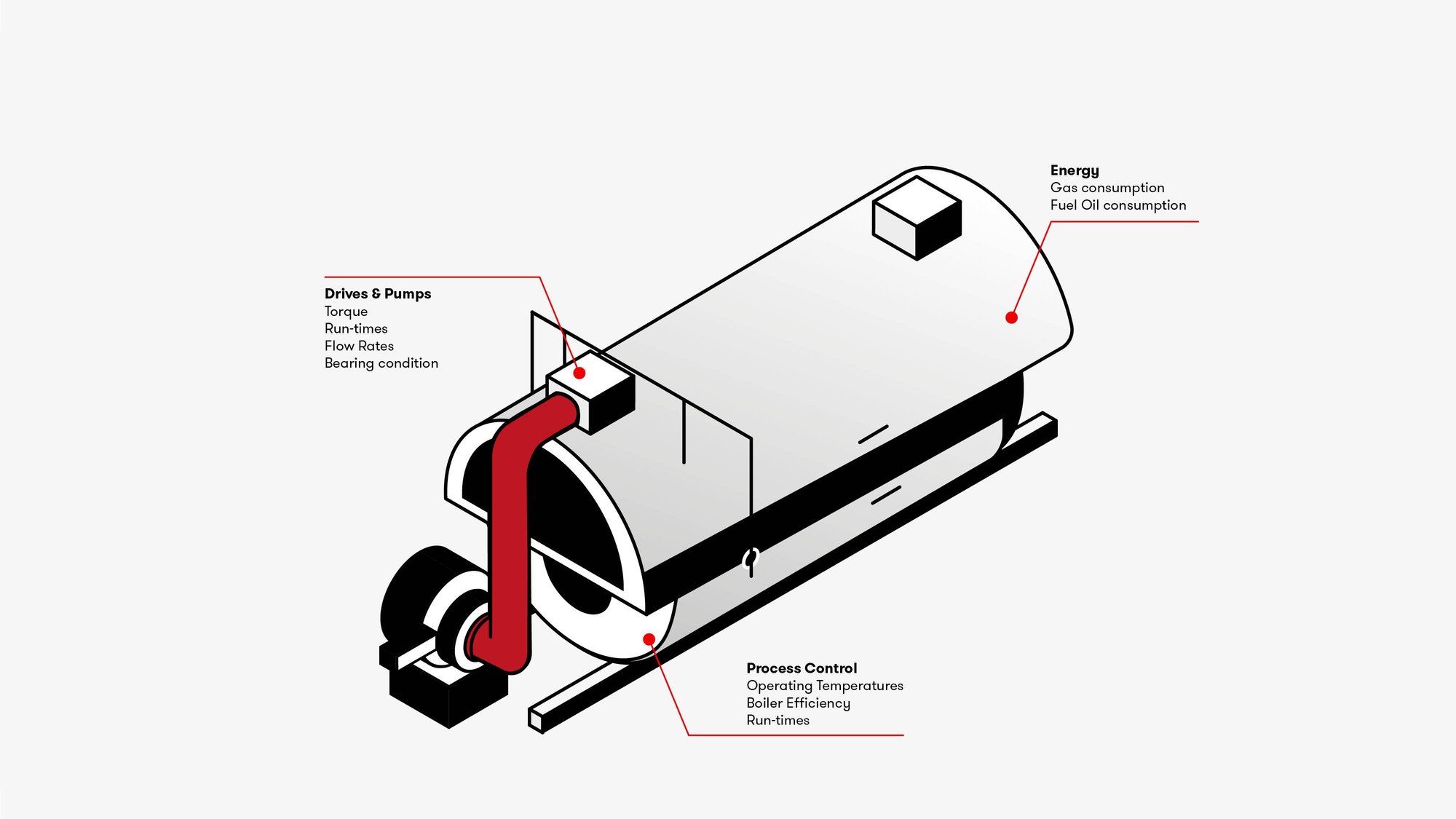
Potential Savings using RS Industria.
£0
Potential Savings in Energy Costs
£0
Reduction in Maintenance Costs
£0
Reduction in Operation Costs
Overview
Fire tube boilers are widely utilised in industrial settings to generate saturated steam, high pressure hot water, or superheated steam.
This is achieved by heating water in a pressurised drum using hot gases generated from liquid or gaseous fuel combustion which circulates through submerged tubes.
RS Industria is your asset monitoring solution that provides a simple, fast and affordable way to closely measure the operating performance of fire tube boilers. Our system monitors the efficiency of drives and pumps, gas and oil consumption, operating temperatures and run-times. This key operating data helps to balance load between boilers, avoid potential breakdowns and reduce emissions.
Energy Consumption
The Challenges
A fire tube boiler can consume its own capital cost in fuel burnt every year and so ensuring the boiler is operating at peak efficiency is key to ensuring cost effective operation, yet many older boilers lack the telemetry to do this in real time. Even where the efficiency is measured, this data is often presented on local HMIs, with the data difficult to access and correlate with other data sets. In addition, the parasitic electrical load from the combustion air fan and boiler-water feed pump can also be high and is often not measured or, if it is, it is measured poorly.
Our Solution
Monitoring of electrical energy from the ancillary assets (pumps and fans) can be easily achieved through CT clamps for older motors or direct from the inverter drive for more modern installations.
Calculating the efficiency of the boiler itself is critical to ensuring low energy conversion losses. Fuel and steam meters are usually present, and the data can be extracted, but these are often not connected to any network and frequently rely on manual reading and recording. Where such meters are not fitted, ethernet-enabled meters can be supplied.
The accuracy of the efficiency calculation can be improved through understanding condensate and blowdown losses. Efficiency of the steam traps can be estimated by monitoring the return of condensate back into the hot well through suitable meters, as can energy lost to blowdown.
Book an Energy Consultation to find out how much you could save!
Your Benefits
A 10 tonne/hour boiler can easily consume in excess of £500,000 of gas per year at (May 2022 prices). A 5% improvement in energy efficiency will deliver a saving of £25,000 per annum.
£25,000 Energy Annual Saving
Operations
The Challenges
Whilst boilers are typically unmanned, where multiple boilers are installed it is key to understand how much time the individual boilers are spending in full-fire, partial-fire or hot standby. This is particularly important where the available boilers have a range of different efficiencies: you want to know your most efficient boilers are carrying the majority of the load.
Our Solution
Operational data can be inferred from the fuel and steam meters, giving a good indication of running hours and percentage load.
Your Benefits
Balancing load between boilers to ensure the most efficient unit is running at any point in time could deliver a further 5% reduction in energy consumption, or an additional saving of £25,000 per annum
£25,000 Operation Annual Saving
Maintenance
The Challenges
Whilst generally highly reliable assets, hence the reason they are in such common usage, fire tube boilers do suffer from a number of potential drawbacks that can severely impact their operational efficiency:
- Reduced thermal conversion efficiency due to poor setup
- Corrosion or scaling due to inappropriate water chemistry treatment
- Failure or degradation of ancillary devices such as feedwater pumps and air blowers
- Blocked steam traps
Our Solution
The ancillary plant can be simply monitored through tracking the electrical current consumption from either CT clamps or inverter drives. Where more granularity on the potential failure is required, which can increase the warning time to failure, we would look to use vibration and temperature sensors on the motors, pumps and fans.
This provides real-time data on the assets and picks up leading indicators of failure covering looseness, friction, mechanical impacts and overall asset health. Hardness and pH meters will allow monitoring of the water chemistry.
Your Benefits
A typical failure on the fans or feedwater pump could take 6-8 hours to repair and a further 4 hours to bring the steam back to temperature, leading to a total site shutdown of 12 hours - plus the consequential material write-off for any product in process.
£48,000 Maintenance Annual Saving


Reduce Emissions

Avoid Breakdowns
Improve Asset Reliability
Find out how we can help lower energy usage, enhance reliability and improve operational performance: in a way that is simple, fast and affordable.
Contact Our Experts Today