Industrial Ovens
Industrial ovens are a key asset in food and beverage production, allowing for precise and consistent cooking in a controlled environment. From protecting the uniformity of your products to producing large quantities at a faster rate, you rely on your industrial ovens to help reduce production costs and increase profits – all while protecting worker safety and energy use.
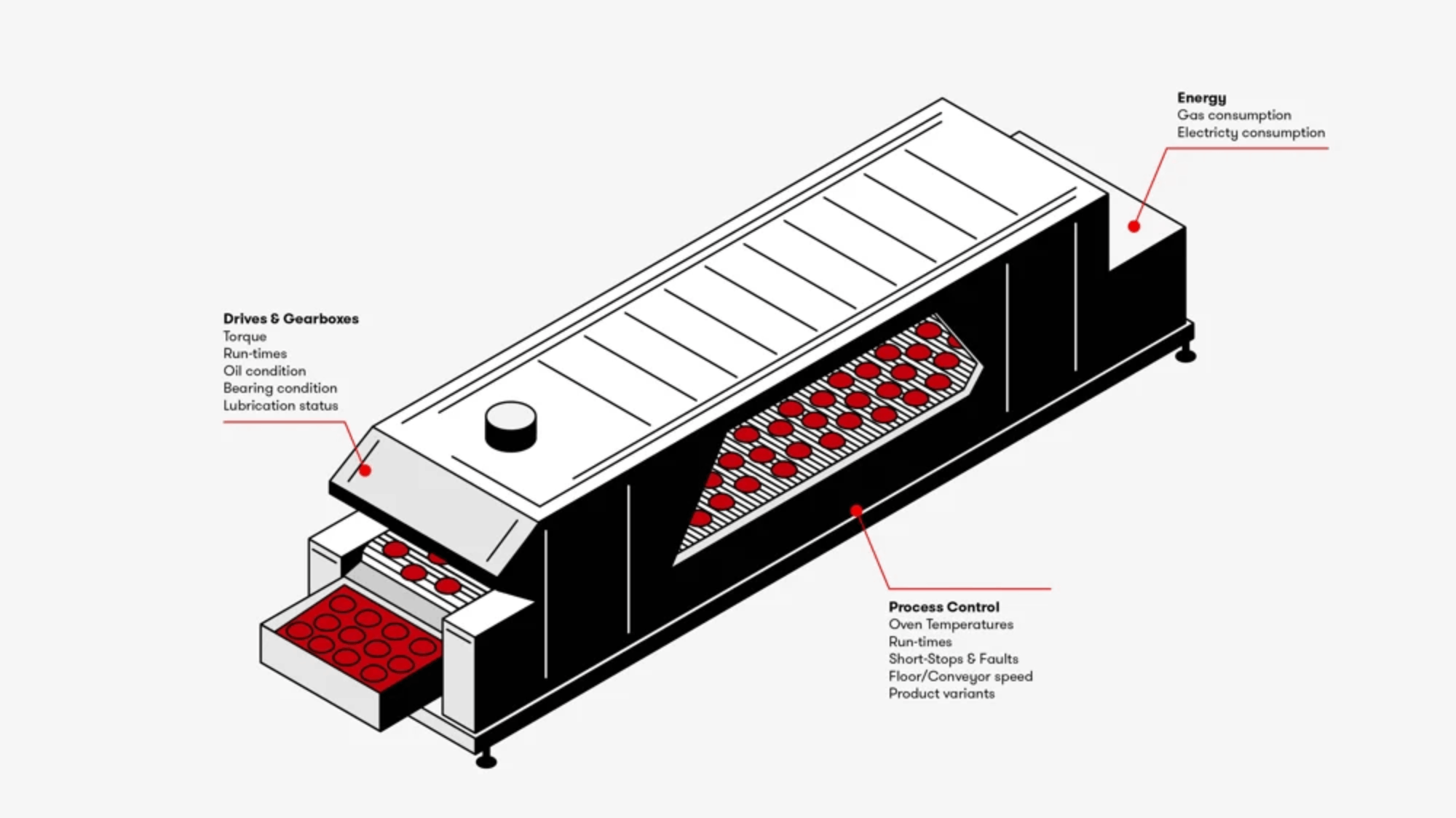
Potential Savings using RS Industria.
£0
Potential Savings in Energy Costs
£0
Reduction in Maintenance Costs
£0
Reduction in Operation Costs
Overview
At the heart of commercial baked goods production is the bakery tunnel oven. Used to produce a wide range of baked goods, bakery tunnel ovens are often combined with an extruder or depositor, which measures out and places batter, dough, or raw product onto the line before it moves into the oven.
Powered and heated by electricity or gas, ovens can transfer heat through convection or radiation, or a combination of both. They use a range of different conveyor types including grids, mesh, steel band, and stones.
Though modern ovens often incorporate a user interface displaying information on settings, maintenance, and energy usage, many legacy assets do not offer easy access to data. Even the intelligence gathered on newer models isn’t necessarily linked up with other data sources from the line.
Energy Consumption
The Challenges
Bakery tunnel ovens can use a significant amount of energy. Without access to data insight, it can be difficult to track how much electricity or gas your oven is using at any one time, which can impact on quality and cost you money.
What’s more, it can be difficult to establish if the start-up and shut-down procedures are optimised to the production schedule, making it difficult to see if your ovens are running when not necessarily needed. The efficiency of ovens can also deteriorate over time as insulation breaks down or gets damaged.
Our Solution
Using easily installed utility and gas consumption meters, RS Industria connects you to the data needed to drive down your oven energy usage and consumption. With the potential for further insight from the PLC and via inverters on conveyors and fan motors, RS Industria enables real-time visibility of a range of data streams, which can be used to track energy consumption and trends and give you the information you need to optimise and align your operational procedures.
RS Industria can also identify if and where excess energy is being lost using a thermal survey; particularly useful in older assets where insulation may have deteriorated.
Your Benefits
A 1 tonne/hour oven will consume at least £400,000 of energy per year.
Mechanical and control issues, combined with insulation breakdown, can reduce efficiency by 10%, increasing energy costs by £40,000 per annum.
Using RS Industria to deliver insight into your usage and identity wastage can drive down costs.
£40,000 Energy Annual Saving
Operations
The Challenges
When an oven isn’t working optimally, incorrect speed, temperature, and depositor rates can all lead to high product loss. To ensure quality products at the end of the process, it is essential the oven is set up correctly. This is particularly important commercially when ovens are used to bake different types of goods.
As ovens are the rate-limiting step on a bakery line, accurate information on performance losses around start-up and shutdown is critical to reducing changeover times and increasing production capacity. In general, reducing changeover times by understanding the rate of thermal change inside the oven and optimising to this parameter, by 1 hour in 24, increases line output by 4.2 percentage points.
Our Solution
Process status data such as running, stop, fault, and waiting can often be captured directly from the PLC. This insight can be used to determine accurate downtime recording and problem-solving.
Further setup parameters can also be captured, which can enhance your ability to solve production issues and assist with operator handover or training.
Your Benefits
By gaining greater visibility and understanding of quality issues during baking, you could avoid the possibility of having to scrap a batch of batter at a potential cost of more than £3,000 per tonne.
Put into perspective, saving just two batches of batter in year 1 would pay for RS Industria set-up and monitoring costs.
£6,000 Operation Annual Saving
Maintenance
The Challenges
Should a high-value asset like your oven fail, the result can be costly in terms of time and wasted product. While engineers need to wait for the oven to cool before maintenance can be carried out, the current batch of products will also likely need to be scrapped. With bakery tunnel ovens often in constant use, engineers have limited windows to undertake thorough inspections and maintenance. Furthermore, time-based maintenance tasks can often introduce maintenance induced failures, while periodic condition monitoring can miss key failure mode leading indicators and is of little use when failures occur between condition monitoring visits. Maintenance can also be hazardous due to the risks of working at height and in enclosed spaces.
Our Solution
A typical breakdown could result in 48 hours of lost time while the oven cools, repairs are carried out, and the oven is brought back to temperature. At an operating and opportunity cost of £1,000 per hour, such a breakdown would result in a £48,000 loss.
Utilising valuable insight from RS Industria can avert catastrophic breakdowns and reduce both spares spend and production downtime.
Your Benefits
By gaining greater visibility and understanding of quality issues during baking, you could avoid the possibility of having to scrap a batch of batter at a potential cost of more than £3,000 per tonne.
Put into perspective, saving just two batches of batter in year 1 would pay for RS Industria set-up and monitoring costs.
£48,000 Maintenance Annual Saving


Enhance Safety

Save Costs
Empower Your Factory
Find out how we can help lower energy usage, enhance reliability and improve operational performance: in a way that is simple, fast and affordable.
Book A Demo