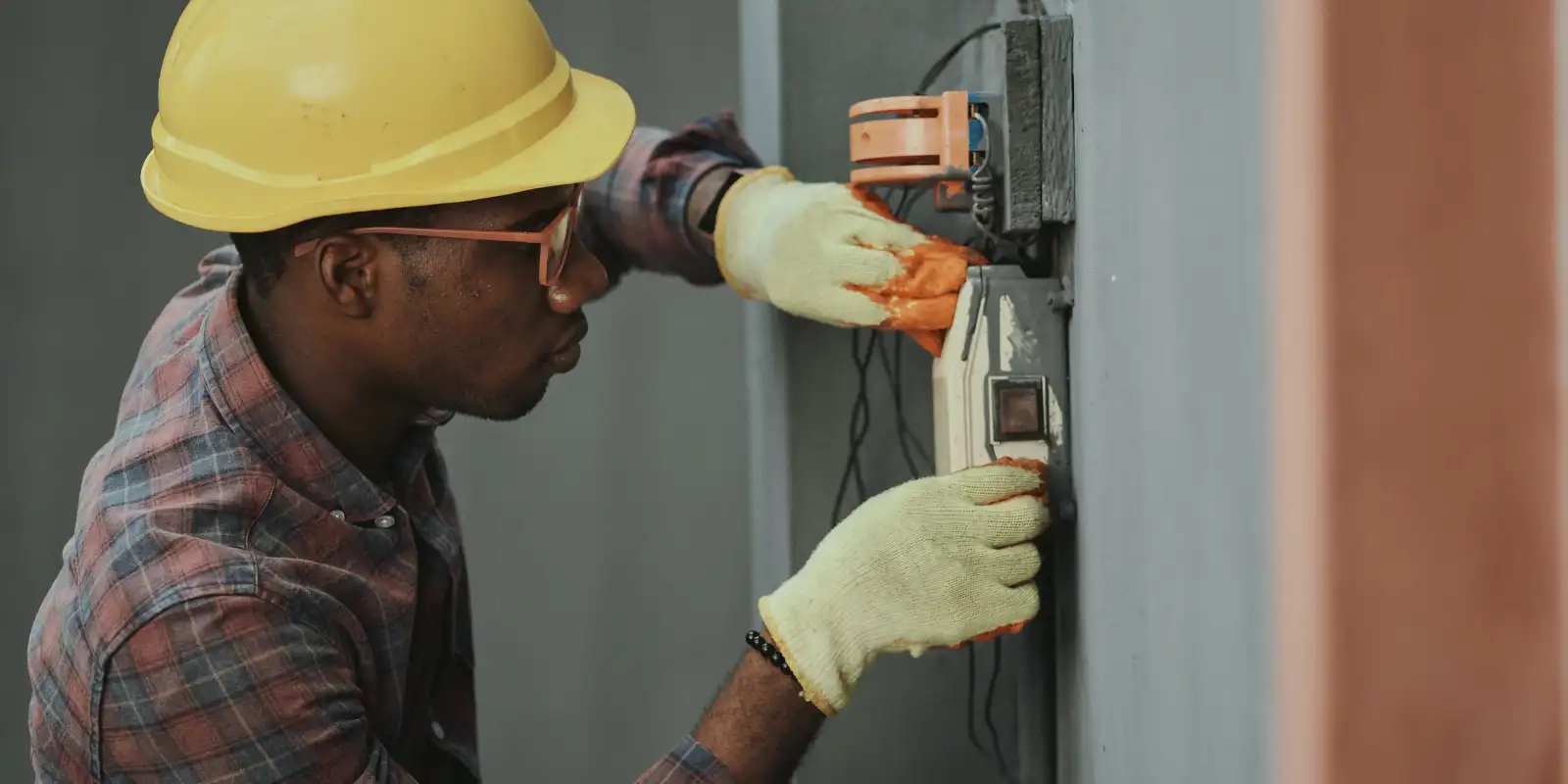
Maintenance engineering teams are a vital element of the drive towards net zero within UK manufacturing
While industry has a critical role to play in achieving globally agreed environmental targets, the economic climate has changed enormously since those goals were approved, with interest rates, inflation and energy prices all sky rocketing.
Research from the manufacturers’ association Make UK, however, indicates that British businesses, particularly large organisations that operate across multiple sites, remain committed to their net zero ambitions. Sixty five percent of survey respondents, for example, have taken positive action towards their net zero targets since COP26 in November 2021.
Nine out of ten manufacturers are planning to take further action
Other findings contained within the report reveal that although only slightly more than one-third of businesses have developed a comprehensive net zero strategy and are beginning to implement it (35%), nine out of ten manufacturers are planning to take further action on net zero and a quarter believe this will lead to more commercial opportunities within high-value green markets.
More than three-quarters say cutting energy costs within their facilities is their main net zero target (77%) and almost half are investigating how to make their production process more energy efficient (48%).
This focus on slashing energy consumption puts maintenance engineers at the heart of net zero goals, responsible for reducing both carbon emissions and energy costs.
Start with strategy and simplicity
Why are maintenance engineers so crucial to cutting energy consumption within manufacturing plants? Because leaks, insulation and thermal loss account for more than half of industrial energy waste.
The most effective way to address this issue is by developing a comprehensive energy management strategy that considers energy efficiency in conversion, distribution and consumption.
Cut energy expenditure by up to 25% by installing energy efficiency measures
This doesn’t have to be overwhelming. You can start with simple changes to reduce carbon emissions, many of which reduce energy costs too. According to government figures, for example, the average small and medium enterprise could cut its energy expenditure by up to 25% by installing energy efficiency measures – and 40% of these savings require no capital expenditure.
Quick wins include steps such as installing LED lights, which use as much as 90% less energy than standard bulbs and have a longer life, or reducing motor speeds by 20%, which lowers power consumption by up to 50%.
Cut system run times within compressed air systems by sealing leaks. Identify more opportunities by commissioning a site-based energy-loss survey that finds the most significant areas of wastage and where energy consumption can be reduced.
Introduce condition-based monitoring
Alongside relatively simple changes, your energy management strategy may include bigger commitments such as a programme for introducing condition-based monitoring of equipment.
Condition-based monitoring involves connecting digital sensors to machines to generate data on performance. By analysing that data, maintenance engineers can locate exactly where energy is being wasted, address the causes of waste and thereby reduce carbon emissions as well as energy bills and the cost of unplanned downtime.
“Increased energy consumption is frequently linked to maintenance issues”
Richard Jeffers, founder and Managing Director, RS Industria
“Increased energy consumption is frequently linked to maintenance issues,” says Richard Jeffers, founder and Managing Director of RS Industria, a plug-and-play Industrial Internet of Things (IIoT) platform. “If electricity consumption goes up it can be caused by an electrical or mechanical fault on a machine or in a system.
“Monitoring energy use can be a leading indicator of an impending failure. If you get your energy monitoring right, you will have higher levels of availability on your plant as well.”
Keep to those key metrics
Net zero strategies may be a new priority within the world of manufacturing, and digitally enabled condition monitoring may be a recent innovation too, but the underlying mechanisms for both are familiar to maintenance engineers.
“Key metrics for maintenance engineering…are critical for reducing energy consumption”
Dr Moray Kidd, maintenance engineering academic
As maintenance engineering academic Dr Moray Kidd explains, “Some of the key metrics for maintenance engineering – availability, reliability and operational performance – are critical for reducing energy consumption.
“If you do maintenance engineering well, you are keeping your assets in the best condition and they’re running at maximum efficiency. Operational expenditure is also more sustainable because you’re not changing components based on a preventative schedule. You’re changing them based on the condition.”