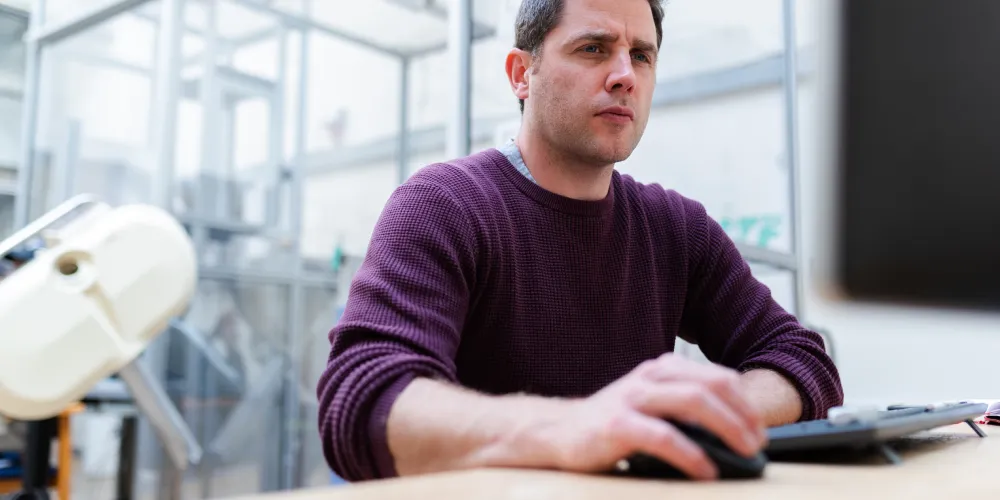
A planned approach to maintenance boosts resilience, allowing your maintenance engineering team to undertake reactive maintenance more effectively too
Being able to keep a cool head in a crisis is a useful skill, especially for maintenance engineers who deal with unexpected machinery breakdowns that be costly if downtime can’t be kept to a minimum.
Another useful skill is the ability to plan a maintenance engineering programme that minimises the risk of unplanned and expensive outages in the first place and frees up more time and capacity to undertake routine maintenance on a rolling basis.
Increased resilience
The benefits of a planned approach to maintenance are enormous.
“If your maintenance organisation is 100% shift-based then it’s designed to react to failure,” says Richard Jeffers, founder and Managing Director of RS Industria, a plug-and-play Industrial Internet of Things (IIoT) platform. “The result will be very poor compliance with your planned work and from that more failure will follow.”
A planned programme, however, makes your organisation more resilient. As well as fewer failures and less downtime, the maintenance team will have the capacity and capability to react quickly when an unexpected problem does arise. Together, this creates more value for the business. It also gives the maintenance engineering lead more leverage when requesting resources to support the further development of maintenance operations.
Strategic support
Although a planned maintenance programme is important in and of itself, it needs to be part of a wider strategy for resilience too – and both need continual revision to ensure they’re as effective as possible.
“Some key questions arise when building and operating a planned maintenance schedule,” explains Jeffers. “Does your strategy ensure that labour, spare parts and any specialist contractors are available when you need them?
“Ask yourself if the planned maintenance you’re doing is improving asset availability”
Richard Jeffers, founder and Managing Director, RS Industria
“When the time comes for a review, ask yourself if the planned maintenance you’re doing is improving asset availability. Interrogate the data to find out if you are reducing the amount of maintenance-induced failure.”
Maintenance engineering academic Dr Moray Kidd also believes that a well-planned and well-executed strategy that incorporates planned maintenance is crucial for building resilience. “There have been a lot of advances in the last 20 years around condition-based or predictive maintenance, with machine learning and more elaborate methods used for those assets that are more critical,” says Kidd.
“Preventative maintenance is by far still the most common practice where assets are maintained, based on operating hours or another more appropriate metric.”
Bespoke solutions
Unfortunately, even the most robust planned maintenance programme cannot eliminate all risk of unforeseen breakdown, particularly in complex manufacturing facilities.
“Maintenance strategy should have a mix of different approaches”
Dr Moray Kidd, maintenance engineering academic
Engineers must therefore remain ready to respond to incidents quickly, acknowledges Kidd.
“Maintenance strategy should have a mix of different approaches,” he states. “Often people think that reactive maintenance is a practice that is no longer appropriate – but it’s not that simple.
“For items that are less critical, run-to-failure may still be the most appropriate option.”
Think about the approach that best suits the needs of your organisation, advises Kidd. “A lot of these strategies depend on the type of industry and the type of operation,” he continues. “They’re all relevant provided they are applied appropriately, in the right place, at the right time.
“When that happens the outcome is resilience within the business, whether that's improving reliability or reducing the downtime through clever planning.”
Engage stakeholders
Successful implementation a new approach to maintenance may require a change of mindset for all involved. “You’ve got to differentiate your maintenance execution into planned and reactive work,” says Jeffers, “and you've got to emphasise the importance of sticking to the plan.”
“Your people are central to a robust maintenance plan”
Ian Bell, Vice President of Engineering and Facilities, RS Group
This can be unsettling for the maintenance engineering team, admits Ian Bell, Vice President of Engineering and Facilities at RS Group. Overcoming doubts and resistance to new ways of working involves good leadership. “Your people are central to a robust maintenance plan,” emphasises Bell. “They must be highly engaged and willing to back processes that are intuitive and clearly defined.”
Commit and recommit
Furthermore, when an expected failure inevitably does occur, maintenance engineering managers must ensure that their team doesn’t return to previous ways of working. On the contrary, is after undertaking reactive maintenance that the planned maintenance programme needs reinforcing the most.
“Most breakdowns are exceptional, or you've seen them before,” says Bell. “What you’ve got to do is make sure you don’t overreact to them. Don't over-steer to control the skid.
“It’s so easy to get distracted by what’s happened and you lose sight of the plan you had. Deal with the crisis at hand and then immediately get back to your long-game strategy.”