How RS Industria is helping a food producer achieve sweet success
2 min read
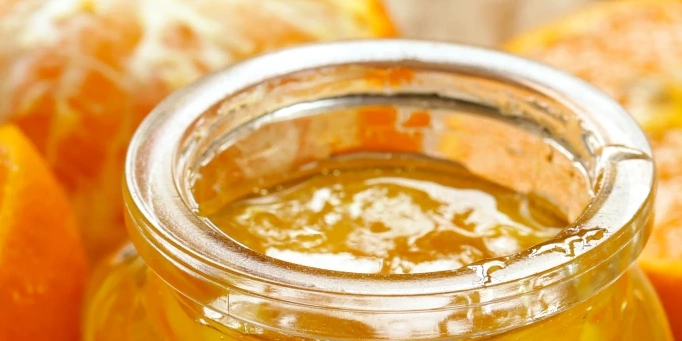
There are some assets that provide a real challenge for maintenance professionals. Components sealed for life upon manufacture are one of them.
For one leading manufacturer, RS Industria’s ingenious system enabled insight into component performance and prevented the potential for catastrophic failure.
The Hain Daniels Group is one of the UK’s leading food companies, manufacturing private-label foods and major brands including Hartley’s, Sun-Pat, and New Covent Garden Soup.
Hain Daniels has eight UK sites employing 1300 people. The business prides itself on its ambition, innovation, and energy, and delivering excellent quality for customers.
Its Cambridgeshire-based Histon Preserves site - the company’s largest - manufactures ambient spreads and jellies, including well-known marmalades from Rose's and Robertsons.
Keeping machines on the move
One of the assets critical to Histon’s output is its high-speed filling machine. To keep the machine on the move, right-angled power transfer boxes connect the main filler to the blower, which ensures that the two key parts are always synchronised.
As the transfer boxes are located under the filling line, they are difficult to reach, making external inspection difficult. With the power box ready-sealed and with no sight glass, getting a view of the internal lubricant levels was impossible for engineers.
Given the potential for corrosion from sugary and acidic food debris, the asset required frequent cleaning. This meant any tell-tale signs of lubricant leakage or water ingress were likely to be washed away by the necessary high-pressure water and steam cleaning of the line.
For Histon’s engineers, who understand the benefits of condition monitoring in maintaining production and the difference it can make to maintenance, there was only one solution – RS Industria.
RS engineers worked with their Histon counterparts to fit several vibration sensors onto key components within the filling line, including the two power transfer boxes.
Continuous condition monitoring was then enabled by digitally connecting the sensors to the RS Industria data platform, which was able to capture information such as line status, short-stops, and run rate.
Automated alerts
To enable automated alerts to be sent to Histon’s engineers in the event of any issues, vibration levels were baselined within the context of the process control data to set up vibration limits.
RS Industria proved its worth within months when it highlighted a significant increase in overall vibration within one of the transfer boxes. With the increase flagged, the site team was able to order spare components as a precaution.
When vibration levels suddenly increased further a few weeks later, the team was alerted to the imminent failure of the transfer box. The filler was stopped to replace the transfer box quickly and efficiently.
Once opened up, the old transfer box revealed damage to the bearings while the sealed lubricant was contaminated with water. The unit had been just hours away from catastrophic failure – an event that would have caused the filler to be shut down for at least two days and cost the customer thousands of pounds.
Using insight to monitor critical assets enables you to optimise your plant and achieve greater efficiencies. Keen to learn more? Contact us today.