High-performing maintenance, high-performing business
4 min read
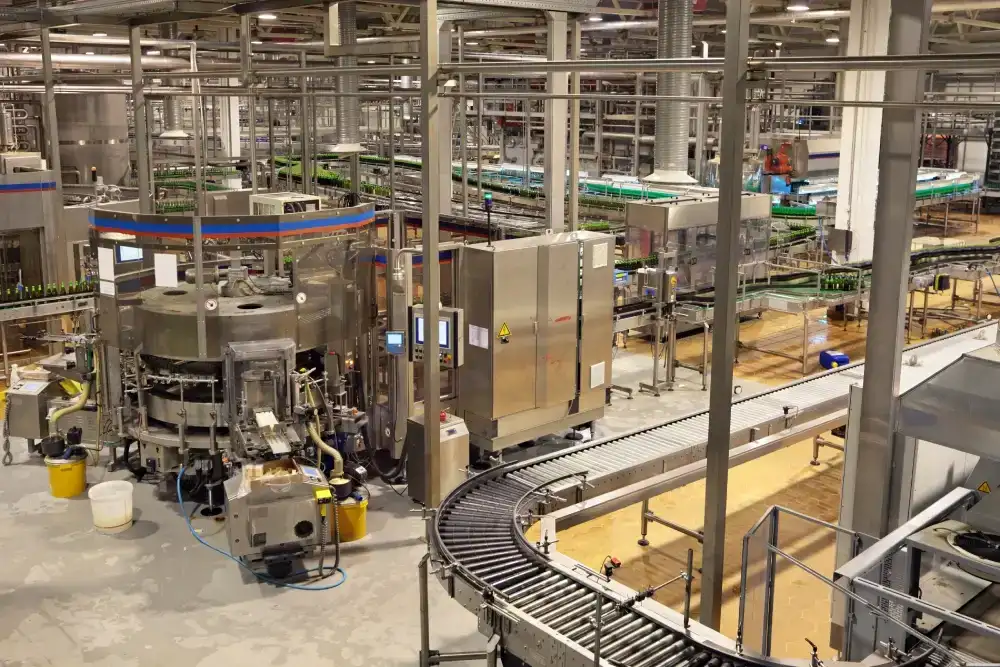
Enabling your maintenance engineers to perform at the highest level helps drive commercial success, but how can you ensure that they flourish?
When conducting research for the report “What High-Reliability Organisations Get Right,” global consultancy firm McKinsey studied high-performing maintenance engineering teams to uncover what exactly set them apart. The answer? People.
Here we share the key takeaways from “What High-Reliability Organisations Get Right” for you and your organisation, beginning with more details about the report’s findings.
Define high performance
McKinsey used three criteria to define success and high performance:
- Outperform competitors on all key business metrics
- Few breakdowns
- Low levels of downtime
The firm used data from its clients to identify manufacturers who fulfilled this remit and from this list selected maintenance engineering teams in industries including mining, energy, power generation and distribution, pharmaceuticals, airlines and the military to study. What made them so successful?
The report found that all these maintenance engineering teams use Industry 4.0 technologies such as condition monitoring and data analytics. However, the most significant factor was people.
Set up systems for success
To flourish, the individuals who make up a team need both expertise and the right structures in place to work at effectively.
“Technology alone does not make for excellence in reliability”
McKinsey, “What High-Reliability Organisations Get Right”
As the report states, “Technology alone does not make for excellence in reliability. In industries that live by the laws of science, leaders often underestimate the role of management processes and skills in reliability engineering.”
What does this look like in practice?
McKinsey’s analysis showed that all the highest performing firms had well-defined lines of accountability, robust maintenance processes and clearly delineated roles and responsibilities for every member of the maintenance engineering teams.
McKinsey found, for example, that these teams closely monitor asset performance, using data and their own expertise and experience to establish the underlying cause of every failure. Doing so reduces the risk that the same failure will happen again.
By updating work processes after every incident of breakdown, maintenance engineers share what they’ve learnt with the rest of the team. This knowledge sharing, and strong systems to preserve it, contributes significantly to team success.
Clarify purpose and processes
These findings come as no surprise to Richard Jeffers, founder and Managing Director of RS Industria, a plug-and-play Industrial Internet of Things (IIoT) platform. Clarity of purpose is crucial, he says.
“Everyone in the maintenance engineering team needs to understand what they are there to do. So, communication is absolutely critical. It’s not surprising if operational colleagues get frustrated if we’re unclear about what we’re here for,” he explains. “The purpose of a maintenance organisation is keeping operational assets in the hands of the user at least cost.”
“Robust maintenance process is about people”
Ian Bell, Vice President of Engineering and Facilities, RS Group
Ian Bell, Vice President of Engineering and Facilities at RS Group, agrees. “Robust maintenance process is about people – the great team that are highly engaged with processes that are known and defined and intuitive,” he says.
Like Jeffers, Bell also believes that people need a clear structure to operate within if leaders are to get the best out of a team. “You need great people, but great processes, too,” he continues. “You’ve got to understand what you do. How you deploy your staff, how you manage your priorities and tasks, and having them clearly defined is really important, too.”
Reward performance with pay and progression
Recruitment and retention play an essential role in building a strong maintenance engineering team. “Attract and retain great people,” urges Bell. “Make sure you engage them and create that bit of passion and enthusiasm.”
“If the company wants excellence or world class, they have to pay for”
Ian Bell, Vice President of Engineering and Facilities, RS Group
“You need to be smart, but it does need money. You can’t do it on a shoestring – if the company wants excellence or world class, they have to pay for it,” he adds.
The findings from McKinsey support Bell’s claim, with the “What High-Reliability Organisations Get Right” study reporting that good pay is an important element in building a successful maintenance engineering team. It stated that “Salaries at the high-reliability organisations – average, as well as the low and high end of pay scales – were 15% higher than those of their peers.
“Some also had performance-based pay and bonuses based on uptime.”
McKinsey discovered that opportunities for career progression are vital for maintaining motivation too, with the highest performing companies having promotion routes that allow engineers to move into roles as subject matter experts for the whole company.
Dr Moray Kidd, a maintenance engineering academic, also believes that opportunities to progress are extremely valuable. Maintenance engineers need senior role models who demonstrate how they can advance, he says, but he thinks the UK may be lagging on this.
When it comes to putting engineers into the top leadership roles, Kidd contrasts his experience of working for a major German firm with the situation in the UK. In Germany, says Kidd, “It’s quite normal for engineers to be managing directors and decision-makers within organisations.”
Adjust your mindset
As well as working to improve opportunities for career progression, companies also need to adjust their mindset about what successful maintenance engineering looks like – and greater recognition of the value of predictive maintenance is a good starting-point.
“The idea of looking at the outputs of your actions and then using that to drive future actions and do it better next time, is not new,” says Jeffers. “We’re not suddenly much cleverer in the twenty-first century than they were in the previous one.
“I think what’s fundamentally changed in maintenance is a recognition that data can drive your maintenance strategy. And if you understand failure modes, failure theory and the leading indicators of failure then you can start to use that understanding to drive your maintenance strategy in a structured fashion.
“Value the engineer who stays calm because they’re in control”
Richard Jeffers, founder and Managing Director, RS Industria
“At the same time, you’ve still got to get people to respond to the data and to value the engineer who stays calm because they’re in control, more than the hero who runs and fixes that machine at two o’clock in the morning. Sadly, many businesses are still rewarding the hero culture, rather than the analytical one.”
“Good maintenance engineering does not cost you: it should pay you”
Dr Moray Kidd, maintenance engineering academic
This shift will also help senior leaders to see how effective maintenance engineering contributes to business success. “Maintenance engineering has historically been seen as a sort of an overhead,” says Kidd, “But I think going forward, people will come to appreciate that good maintenance engineering does not cost you: it should pay you. And so, if it’s done well, it’s a sound investment.”