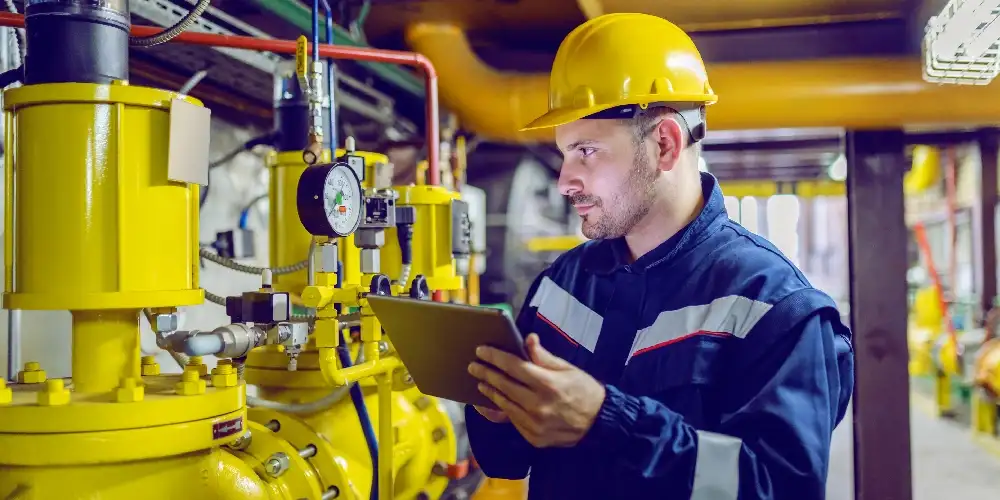
Engineering is changing – and fast. Embracing digital transformation now will help engineers and manufacturers to adapt for the future
Have a problem that needs solving? Ask an engineer. The biggest challenge they face right now, however, is the rapid pace of change within engineering itself. Developments in technology, for example, are transforming collaboration and innovation as well as the product creation process.
The Institution of Mechanical Engineers (IMechE) and the Institution of Engineering and Technology (IET) recently commissioned a survey of manufacturing engineers to get a better understanding of the speed of transition. The result? Most expect “major change” within five to ten years.
What does this future of engineering look like? Industry experts share their views about the changes we can expect – and how can engineers and manufacturers can adapt.
Engineers as business leaders
Engineers rarely work in isolation – but wherever you have a team, you also need a team leader. These leaders will play a crucial role in the change management process.
“You can’t delegate digital transformation for your company,” states Barry Ross, a US change management specialist. “You and your executives have to own it! Executives need to engage, embrace and adopt new ways of working with the latest and emerging technologies.”
“Transformation really needs to be driven from the top”
Mohamed Abdelhak, strategic account manager, Autodesk
Mohamed Abdelhak, a strategic account manager at engineering software company Autodesk agrees, telling an IMechE Engineering Futures event that “Transformation really needs to be driven from the top. Executive-level buy-in isn’t enough...what is really needed is executive leadership.”
At present, 15% of CEOs at FTSE 100 companies come from an engineering background. To maintain this presence, or even boost it, engineers who aspire to senior management roles need to ensure they have the right attributes to lead change. According to the report from IMechE and IET on the future of engineering, it is the so-called soft skills of communication, creativity and design thinking that will be crucial.
Widespread digitalisation
The growth of Industry 4.0 will also be crucial.
Use of the Industrial Internet of Things (IIoT) to leverage data in support of process optimisation and product development is already changing engineering and this will only intensify.
The problem, says global consultancy firm McKinsey, is that thus far most companies have only introduced Industry 4.0 technologies in a piecemeal fashion. By failing to join up the different elements and getting them to work together, the same organisations remain stuck in “pilot purgatory.”
“Companies at the front of the pack are capturing benefits across the entire manufacturing value chain”
McKinsey
“While digital transformations are notoriously difficult to scale up across networks of factories, the pressure to succeed is intense,” write McKinsey experts, “Companies at the front of the pack are capturing benefits across the entire manufacturing value chain. Scaled across networks, these gains can fundamentally transform a company’s competitive position.”
It is easy to see why when you look at the results that successfully collating and analysing data from IIoT devices across a digitally enabled factory can produce. McKinsey reports up to a 50% reduction in downtime as well as an increase in throughput of nearly a third and 85% more accurate forecasting.
Clearly defined digital projects
How can more organisations capture the benefits of digital transformation across the whole manufacturing value chain?
They will need engineers with the right knowledge and expertise, which the IMechE and IET report lists as skills in automation, robotics and mechatronics as well as artificial intelligence and resource-efficient lean manufacturing.
Communication with stakeholders is critical too, advises McKinsey. The project must also focus on real business needs and build on technology solutions that have already worked in the organisation.
Moreover, companies need to think through a plan and avoid the temptation to jump in headfirst.
“There is no value in launching a digital transformation unless you are clear on the benefit you want to achieve”
Richard Jeffers, founder and managing director, RS Industria
Richard Jeffers, founder and managing director of RS Industria, a plug-and-play IIoT platform, offers similar advice. The best starting point for creating a plan is to identify what real-world problem you are trying to solve, he argues.
“There is no value in launching a digital transformation unless you are clear on the benefit you want to achieve,” says Jeffers. “It might be around data and using IIoT to support the identification and eradication of losses. It might be around productivity and using robots to automate repetitive tasks.
“It might be around learning and development and using augmented reality to give workers access to support documentation in the workplace. But there has to be a driver!”
Digital transformation as a process
One of the major challenges, however, is that many organisations simply do not have the bandwidth required to develop an over-arching digital strategy.
In his role as CEO of Velocumen, a business that advises companies on IIoT and Industry 4.0, Ian Clarke visits many firms and notes that in almost every case, “None of the machines are connected to a site-wide digital strategy.
“There’s no end to the benefits that a digital transformation can bring to this business if managed correctly”
Ian Clarke, CEO, Velocumen
“I visited one such company recently. Their energy bill is £250k per month, on a £20m turnover and the bill has tripled in the last six months. There’s no end to the benefits that a digital transformation can bring to this business if managed correctly.
“They have committed to, and just embarked on, their connected operations journey, but are struggling to get started. But they do have a viable plan which is to build the digital infrastructure and then start with an easy-to-deploy, easy-win project.”
Easy win projects are a great place to begin with IIoT, although that’s often not where an organisation will start. As Mike Wilson from the British Automation & Robot Associationn told an IMechE audience, “Many businesses are looking for the most complex application they have, rather than the simplest job...that may be a great opportunity to install your first robot system.
“You may then find other opportunities to look at more complex applications.”
“Think of digital transformation less as a technology project to be finished than as a state of perpetual agility”
Amit Zavery, head of platform, Google Cloud
Google Cloud’s head of platform, Amit Zavery, made a similar recommendation in a Twitter post. “Think of digital transformation less as a technology project to be finished than as a state of perpetual agility, always ready to evolve for whatever customers want next, and you’ll be pointed down the right path,” he wrote.
Wholescale automation as a long-term goal
This advice is especially pertinent to the small and medium-sized businesses that make up 99% of UK manufacturing and account for 58% of manufacturing employment, according to figures from the manufacturers’ organisation Make UK.
Figures from Make UK also demonstrate that four in ten small engineering companies are both fast-growing and have the potential to become far bigger. Known as scale-up firms, they contributed £1 trillion to the UK economy in 2020.
Industry 4.0 and IIoT technologies can support their growth. The UK’s Manufacturing Technology Centre (MTC), for example, has developed use cases to demonstrate how a regular electronic manufacturing factory can be converted into a smart factory using its legacy machines, not expensive new equipment.
“Our goal is to showcase products going through a state-of-the-art digital production line, collecting data from each station and machine, creating visibility and showing the value that can be obtained from the many uses of the data,” explains MTC technology specialist Naim Kapadia.
“Digitalisation can now be achieved using interoperable standard components”
Naim Kapadia, technology specialist, MTC
“It is essential for industry to understand that digitalisation can now be achieved using interoperable standard components, which yield immediate results and short-term returns on investment, which are best seen to be believed.”
Even if wholescale transformation remains a step (or several steps) too far in the short term, it can be a valid goal to aim for down the line. Business process consultancy SQA reports, for example, that companies who have embraced automation are seeing lower costs, higher quality, reduced risk, improved productivity and better customer satisfaction as a result.
Automation can also lead to annual productivity gains of 2% to 3%, says McKinsey, although Coca-Cola achieved a huge double-digit productivity increase at its operations in Ireland. The global drinks giant analysed data from IIoT devices to find opportunities to improve efficiency – and as a result, the company could produce more with the existing facilities and add new lines to the freed-up capacity.