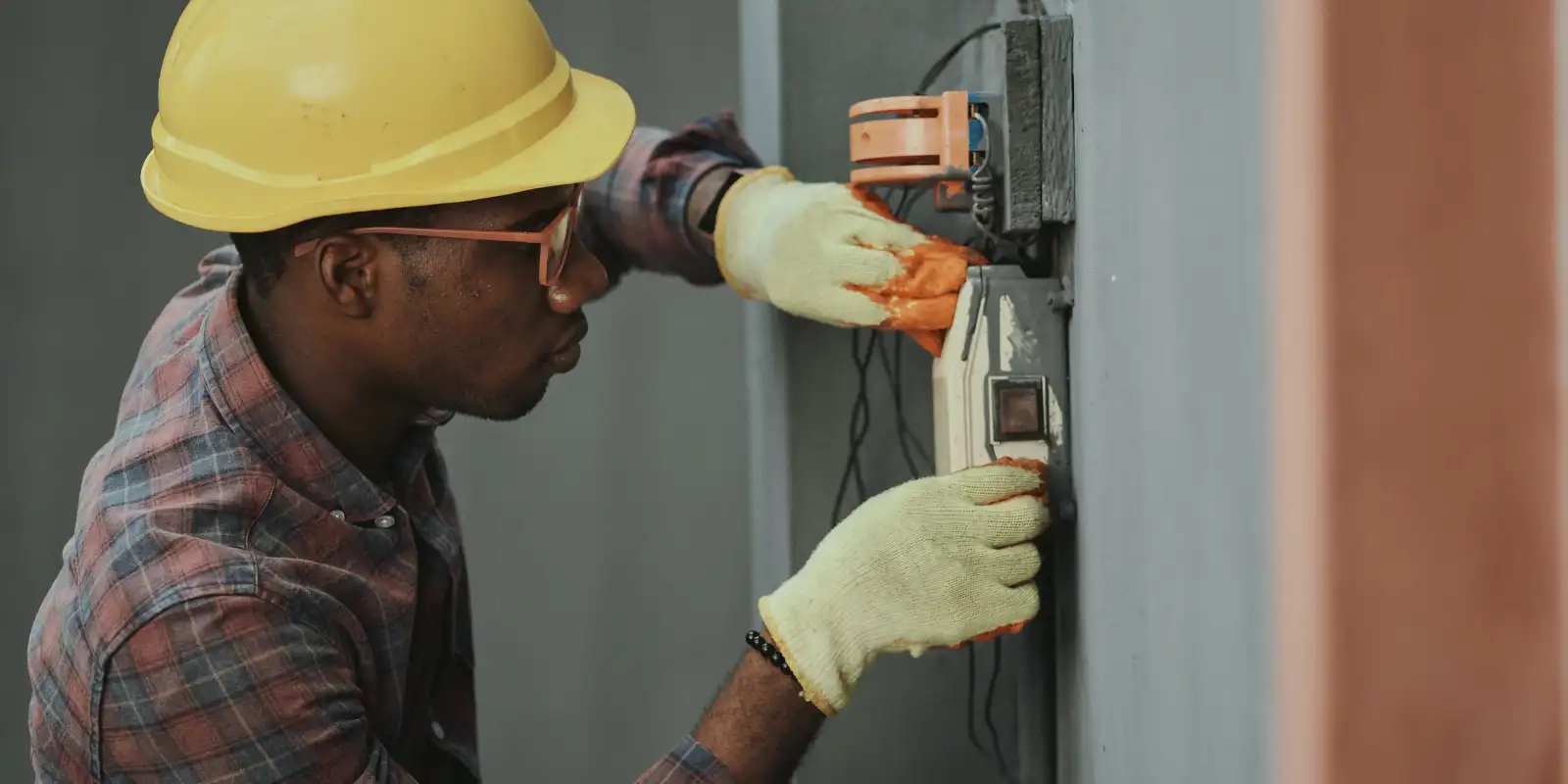
If you’re a maintenance engineering lead, follow these steps to make your operations, team and business more resilient when the next major incident occurs
Analysis by investment platform Interactive Investor reveals that although experts had been issuing warnings about the risk of a global pandemic since 2016, just thirteen FTSE 100 companies included this as a potential threat in their business plans for 2020.
Being caught in a similarly exposed position when the next unexpected event comes along isn’t inevitable. On the contrary, it is possible to prepare for events with a low probability of occurring as well as more commonplace risks that could affect your organisation such as fire, extreme weather and civil disruption.
If you’re a maintenance engineer, the quality of your preparation and planning will determine how quickly you can restore operations to full working order when an incident occurs.
Here’s how to ensure you’re as ready as possible.
- Develop a plan – but make it flexible
Creating a plan for how to deal with major incidents is a crucial first step.
A plan “is absolutely essential, if for nothing else to give some structure early on,” says Ian Bell, Vice President of Engineering and Facilities at RS Group. Why? “Because in the melee of something having just happened, people tend to be like headless chickens, it is a natural reaction and a plan is something to anchor on.”
“The trouble is every scenario is different”
Ian Bell, Vice President of Engineering and Facilities, RS Group
Keep it clear and straightforward, advises Bell. “Where a lot of companies go wrong is trying to over-engineer the plans,” he continues. “They make them too specific to individual scenarios and hope that it gives every answer. The trouble is every scenario is different.”
A large fire that destroys a factory roof, for instance, is very different to a fire in the staff kitchen – so instead of trying to categorise risks, develop a flexible approach that can adapt as the situation requires.
Bell describes this as building a toolbox of actions and responses. “Give yourself software contingencies or additional equipment that you can roll out,” he says. “Create a communication plan so you can keep people informed and identify an emergency team structure to coordinate your response.
“Don’t link your tools to specific scenarios because you’ll need to evaluate your situation and then go to your toolbox and roll them out. But make sure any of the tools you come up with actually work in the real world.”
“The immediate desire is to start fixing things”
Ian Bell, Vice President of Engineering and Facilities, RS Group
When an incident inevitably occurs, begin by protecting whatever has survived and establishing a clear view of the situation. “The immediate desire is to start fixing things,” acknowledges Bell, “but what we need to do is secure and understand it.” Then you can turn to your toolbox and instigate the most appropriate response.
-
Consider what would have helped in the past
As well as thinking about potential disasters, make looking back at previous incidents part of your planning process.
The Royal Academy of Engineering, for example, points out that some of the biggest lessons from the coronavirus pandemic include the importance of stocking critical spare parts and ensuring your supply chains are robust.
Resilience planning now, says the Academy, must therefore include identification of critical elements within your supply chain and where pinch points may occur. Investigate what supplies could be sourced locally if necessary and if buffer stocks are needed for certain items.
- Institute preventative measures where possible
Also consider whether there are any preventative measures that could reduce risk levels.
Site design, for instance, can significantly influence the chances of surviving an incident. “While many businesses have a business interruption procedure – and that’s very useful and really important,” says Gary Harvey, Head of UK Field Services at RS, “it hasn’t often been considered when designing a site in order to prevent some of these things from happening.
“The majority of manufacturing industries, frankly, don’t take it seriously”
Gary Harvey, Head of UK Field Services, RS
“It’s important but I think the majority of manufacturing industries, frankly, don’t take it seriously. And they think, sometimes correctly, that the problems they’re going to get are so rare that it’s not worth investing in.”
- Encourage realism about the likelihood of disruption
Attitudes to risk within your organisation may also need revision.
As the Health and Safety Executive puts it, “Every day, consciously or unconsciously, we all view hazards and evaluate their risks to determine which ones we choose to notice, ignore or perhaps do something about.
“We may take the consequences of some risks for granted and, for others, consider that our own chances of being harmed may be either more or less than the average, depending on the apparent degree of control we have for taking or limiting the risks.”
Given the events of recent years, from the COVID-19 pandemic to the blockage in the Suez Canal, the Russian invasion of Ukraine to extreme summer temperatures, is this attitude still tenable? Maintenance engineering academic Dr Moray Kidd doesn’t think so.
“Low probability, high consequence events…seem to be coming around far too frequently”
Dr Moray Kidd, maintenance engineering academic
“These are often referred to as low probability, high consequence events,” he says. “I’m not convinced that they’re low probability – they seem to be coming around far too frequently for my liking.”
Is it possible to nurture an alternative mindset that takes risks seriously without becoming paralysed by caution and fear?
Yes, argues Kidd, citing a planning tool used in maintenance engineering called bowtie analysis. “It’s called bowtie because on the left we consider the causes that might lead to a disaster,” he explains. “In the middle we have the disaster itself; on the right, we have the consequences.
“It’s a technique that we often use to communicate risk and it’s a really effective way of all the stakeholders thinking about their role in keeping people, the environment and the business safe.”
- Optimise your daily operations
Finally, your business-as-usual maintenance engineering processes can make your organisation more resilient when faced with high risk, low probably incidents.
“If you are performing world-class maintenance engineering…you are setting yourself up to survive a crisis”
Richard Jeffers, founder and Managing Director, RS Industria
Richard Jeffers, the founder and Managing Director of plug-and-play Industrial Internet of Things (IIoT) platform RS Industria, encourages maintenance engineering leads to work through a series of question to evaluate how well everyday operations feed into planning for exceptional events. These questions are:
- Do you have a maintenance strategy? If you don’t, you need one, even if it’s quite simple and straightforward.
- How strong is your maintenance plan? Is everyone following it day to day?
- What’s your plan based on? Is it the manufacturer’s recommended service intervals or do you use data from monitoring your assets to create a predictive maintenance plan?
- Are you making the most of fault reporting to understand where the weaknesses exist in your set-up?
- Do you have a disaster recovery plan? Have you read it? Is it actionable?
- Have you thought about what you would be able to do in reality if the worst happened?
- Do you know which are your critical assets, the ones that will stop the factory or cause a compliance issue?
Jeffers also offers reassurance to maintenance engineering teams that operate efficiently and effectively when it’s business as usual but have yet to be stress tested in an emergency.
“There’s no doubt in my mind that if you are performing world-class maintenance engineering, which is about the relentless identification and eradication of losses, you are setting yourself up to survive a crisis,” he concludes.