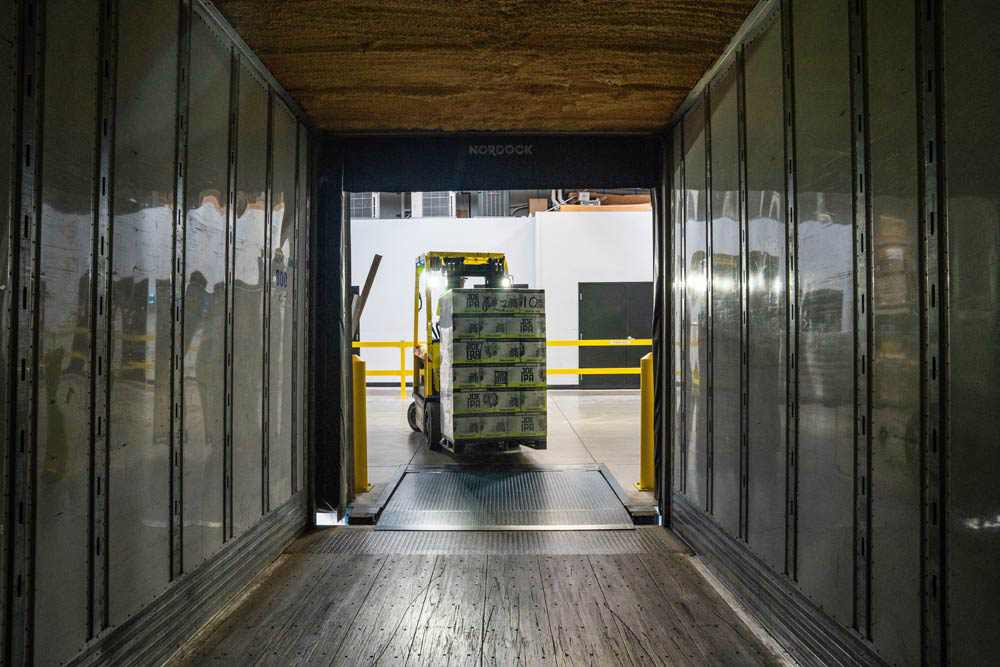
More than half of machinery downtime is caused by hidden internal faults, costing UK manufacturers £180 billion per year.
For one major UK logistics firm, the reasons behind high-wear issues in a critical asset were a complete mystery. Central to its operations, the customer’s parcel sorting machine is a complex unit used to grade parcels by weight and volume.
Custom-designed for the job, the machine has a total of 11 conveyors, consisting of five sorting lanes. Each lane has two conveyor runs to sort parcels before they are then loaded onto a large carousel.
Since the customer first commissioned the machine in 2010, online shopping has accelerated massively. Today, around 14 million parcels are sent in the UK daily.
While the boom has been welcomed by the customer, the increase in parcels highlighted a serious performance issue within the machine.
Excessive wear
Bearings in several gearboxes and conveyor rollers were showing excessive wear and were having to be replaced well before the end of their expected service life. To add to the issues, oil analysis results were showing contamination, which meant the gearbox oil needed to be changed far more frequently than anticipated.
To prevent the potential for costly downtime, or even worse – the outlay for a completely new machine - the customer needed insight, and fast. By implementing RS Industria and connecting to our secure network, the customer was able to better understand the behaviour of each variable speed conveyor drive.
Now, with real-time data showing insight including current, voltage, and power consumption, engineers could get to the bottom of how each of the different conveyors was being used and when.
Mystery solved
Intriguingly it also revealed the hidden issue. To match the sudden increase in parcel volume caused by the boom in internet shopping, previous site engineers had changed the speed of the conveyors, and inadvertently exceeded the machine’s original design capacity. This led to shock load and extra stress on the machine’s components by over-speeding the motor.
Thanks to this insight, the customer was immediately able to reduce wear by reprogramming the drive acceleration profile. With oil samples showing gear teeth wear, engineers were also able to replace the gearbox oil with a better-matched specification to prevent degradation.
By giving the customer greater insight into how the asset is operating, RS Industria data can now be used by the customer to inform tailored maintenance. It’s also given them the tools required for a Monitor & Manage strategy, averting the need for an expensive redesign and rebuild or the headache of a new machine.
Want to optimise your own operations? RS Industria gives you the tools to unlock effective asset management and extend equipment lifespan while driving down factory downtime.