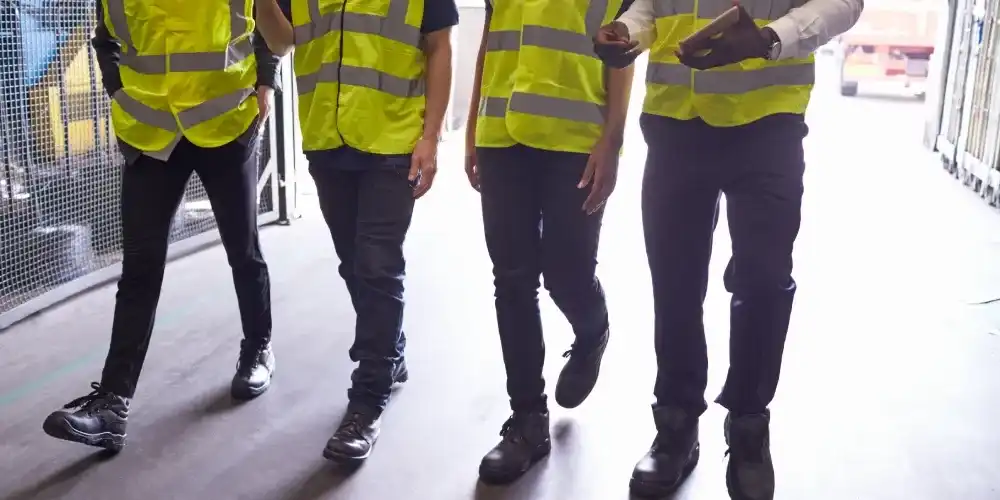
Experts share a six part process for introducing digital transformation into your manufacturing facilities while keeping the machinery running and delivering value.
Although research from global consultancy firm McKinsey demonstrates that digital transformation within manufacturing allows organisations to maintain a competitive advantage over rival businesses, instigating this process remains a daunting prospect – so we asked industry experts to outline a step-by-step approach.
First, understand the problem
The starting point for successful digital transformation projects is clarity of purpose. What is your objective?
As McKinsey puts it, “Future-proofing starts with a clear vision for how digital manufacturing will deliver a competitive advantage, along with a phased road map for implementation based on a business case in which technology is the enabler rather than the driver of change.
“Without this business-first orientation, it’s easy to be led by the latest shiny object rather than focusing on the digital-manufacturing solutions that address specific operational pain points and drive tangible bottom-line impact.”
“Understand the real-world problem you are trying to address”
Richard Jeffers, founder and Managing Director, RS Industria
Other experts working in this space agree. “Understand the real-world problem you are trying to address,” says Richard Jeffers, founder and Managing Director of RS Industria, a plug-and-play Industrial Internet of Things (IIoT) platform.
“There is no value in launching a digital transformation unless you are clear on the benefit you want to achieve.”
Likewise, says Alex Smith, MES Business Consultant at digital manufacturers Cimlogic, a structured approach is vital from the outset. In an article about his own organisation’s approach to future-proofing operations, Smith argues that “It is critical to recognise what the ‘need’ is for a digital solution.
“Uncover what business challenges are causing you the greatest headaches,” he continues. “You must know what business benefit will be delivered and what value or cost-saving will be achieved.”
Second, identify the issues you will face
Once you’ve established what problem you are trying to solve, think through the challenges that you’ll face along the way.
Step back to consider how your organisation operates and map the processes involved as these may not correlate with your understanding of the procedures in place. An issue that Ian Clarke, CEO of digital manufacturing consultancy Velocumen, encounters in many UK manufacturing firms, for example, is the absence of an overall plan.
“What I see in almost every business I visit is that their machines are not connected into a site-wide digital strategy,” he explains. “That’s the bit many big companies really struggle to create: a sensible strategy for how their business is going to find out what’s going on in those machines. What’s their productivity? What’s their overall equipment effectiveness?
“That's just not happening.”
Third, engage the right people in the organisation
To get the kind of board-level buy-in needed to action a digital transformation strategy, you need to clearly demonstrate that it will produce a good return on investment (ROI).
“What are we getting in return in the next two years?”
Ian Clarke, CEO, Velocumen
“Senior management these days are working on such a short ROI window,” says Clarke. “When the head of maintenance engineering says they need to spend £50,000 to start a digital transformation strategy, the board’s response is likely to be well, what are we getting in return in the next two years?”
To answer that question effectively, continues Clarke, maintenance engineering leaders need to understand how board members think and what the wider business objectives are – as well as how their strategy supports those goals. Only then can you clearly communicate the need for investment.
Clarke recognises that this can be difficult. It may involve developing your communication skills. If nothing else, you need to predict what questions you’ll get asked and prepare a convincing argument. Failure to do so may result in delayed implementation and ultimately risk the organisation’s ability to remain competitive.
Think you need help on this front? Check out our guide to writing a compelling business case.
Next, select providers
When it comes to choosing software and hardware providers, Smith advises looking for a partner that will work with you long-term.
Why? Because digital transformation is a journey, not a quick-fix project. This provider says Smith, “should be a company that understands not just the tech but your business, with experience in solving the issues you have.”
“Look at the solutions they’ve delivered”
Alex Smith, MES Business Consultant, Cimlogic
Furthermore, he adds, they ideally should have “experience specific to your industry as often problems are the same within manufacturing, so look at the solutions they’ve delivered.”
Clarke regards this stage as one of the toughest parts of the digital transformation process. You’re likely, for instance, to be continuing with existing plants and equipment. As he highlights, “The vast majority of machines, in all factories, are old by their very nature. In many cases, they’re over 40 years old.” This means looking for solutions that are compatible with your specific legacy machinery.
Then unlock existing data
Your facilities no doubt contain reams of data that isn’t currently accessible – and now is your chance to correct this.
“The cost of that data and the ability to process it has dramatically reduced”
Richard Jeffers, founder and Managing Director, RS Industria
“It’s not that we’ve suddenly discovered that data allows you to do predictive maintenance,” argues Jeffers. “It’s that the cost of that data and the ability to process it has dramatically reduced, because technology can collect and interpret it.”
Unlock that data then analyse it for insights into how to improve maintenance engineering processes and bolster efficiency. Plus, says Jeffers, this data is useful evidence to drawn upon to back your argument about what needs to change.
Clarke agrees, although he also notes that this can be difficult, citing cases where vendors have refused access to the digital manufacturing data that a company has generated. He hopes that such obstructions will soon become a thing of the past. “Companies have to realise,” he says, “that collaboration between machine vendors, rather than competition, is best for industry.”
Finally, continue the journey
One of the great benefits of digital transformation is that it allows your organisation to move into a cycle of continuous improvement.
It’s a journey, remarks Smith, not a destination. You don’t arrive at an end point and then rest on your laurels. The data you’re now seeing enables far more accurate predictive maintenance, says Jeffers, and this is in turn reduces costly breakdowns and downtime even further.