The Benefits

Analysis
Detection of abnormal vibration levels revealed an issue with a bearing at the heart of the filling line.

Visibility
Real-time data enabled immediate investigation
and action before potential damage occurred.
Monitoring
RS Industria utilises continuous monitoring to
eliminate maintenance induced failures and enable a predictive strategy.

Easy and
Affordable
RS Industria is a quick and simple solution, with no significant capital for the customer required.
£0
Avoided costs for replacement parts
£0
Saved in labour costs
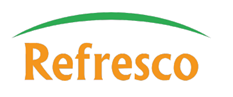
The Problem
At the heart of Bondgate’s beverage packaging operations is one of its most utilised and critical assets - the can filler and seamer. As a complex rotating asset capable of operating at 1,500 cans/minute, failure of the high-speed line can lead to costly downtime and expensive supply chain
interruptions.
As the main bearings used in can fillers are typically manufactured to order, lead times run into months. Visibility of potential degradation of the rotational elements is therefore critical to maintaining production.
With the filler manufacturer’s standard service package coming to an end, Refresco’s engineers needed a solution that would give insight into asset performance and help manage the line’s ongoing maintenance.
The Solution
To monitor ongoing wear and detect potential failures, RS Industria’s team worked closely with the customer to install 14 fixed vibration sensors, covering the main rotating components of the filler.
The individual accelerometer sensors were then connected to RS Industria’s onsite edge gateway via Siemens vibration monitoring cards.
As vibration levels differ with the speed and type of product running through the filler, a baseline was established to consider normal production variances, with alerts triggered when the vibration exceeds what would normally be expected. A customised dashboard was also created to display the vibration data from each sensor on a web-based reporting system.
Within weeks, two of the sensors picked up abnormal vibration levels on the main ring bearing, a crucial and costly element of the asset. This triggered instant alerts to engineers who were able to shut the line down for investigation and resolve a lubrication issue before it could irreparably damage the bearing.
The Outcome
High-speed beverage packaging lines are highly complex and expensive, often costing tens of millions of pounds. Keeping the line running is essential to minimise downtime and disruption, and a key part of this is having visibility of the equipment and its components.
The use of RS Industria reaped immediate results for the customer, revealing detailed insight into the ongoing performance of a crucial asset.
Failure to detect the problem would have led to irreparable damage and stopped the machine, requiring £40,000 for replacement parts, and around £60,000 for labour, plus the loss of finished product capacity during downtime.
"It went rather smoothly; we didn’t have any major issues...the whole process was easy. At the initial meeting with the RS Industria design team, we talked through the information we’d like to see and where we’d like to see it. They showed us what they could offer, and we went for it.”
Karl Hewes, Control Systems Engineer, Refresco Bondgate
Next Steps
The use of RS Industria has enabled Refresco
to move towards predictive maintenance and
helped the operations team improve reliability and efficiency.
As a modular industrial data platform that digitally connects a wide range of industrial equipment for real-time insight, RS Industria can be further expanded to other assets and processes, integrating the site’s entire operations into a single overview.