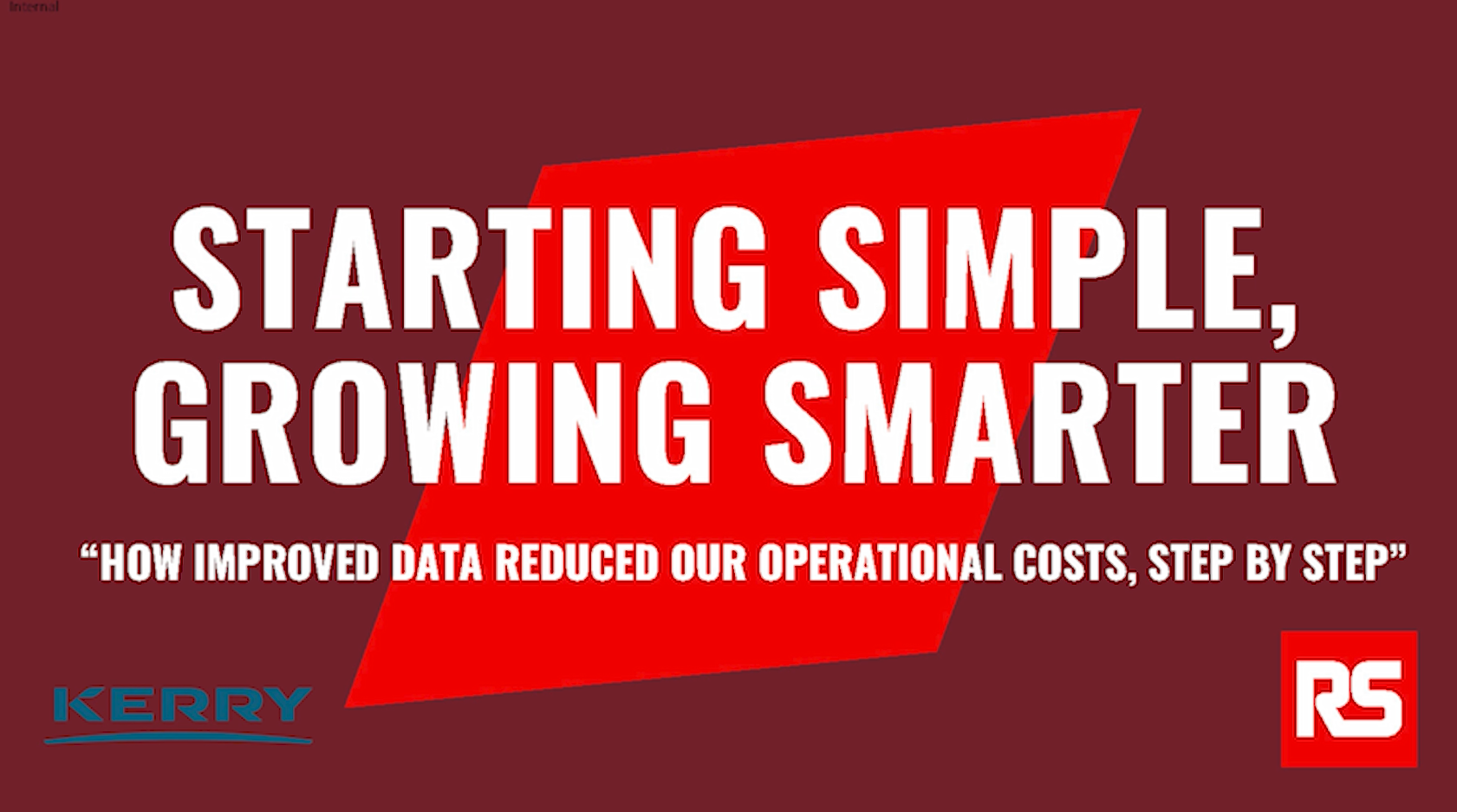
An engineering manager from the food and beverage industry explains how real time data collection and analysis has transformed site maintenance
Ben Botwright, engineering manager at the Kerry Foods production facility in Tetbury Wells, Worcestershire, can tell you exactly why he and his team use the Industrial Internet of Things (IIoT) to monitor the performance of critical assets.
“All of this is about improving manufacturing, reducing our losses, improving our cost performance, ultimately saving money and reducing our environmental impact,” he explained during his keynote address at the Manufacturing and Engineering Week 2023 trade show, held at the NEC in Birmingham in June 2023.
Botwright was on stage to share his experiences of introducing the modular IIoT platform RS Industria to the site, which produces sweet and fruit-based products such as syrups for coffees and fruits for yoghurts. He talked about the challenges that he and the maintenance engineers, working with other colleagues and the RS Industria team, have tackled as part of this digital transformation journey.
Here are some highlights.
Challenge 1: wastewater
What was the challenge?
- Maintaining compliance on a day-to-day basis
- Uncertainty about what the plant was doing on a day-to-day basis and therefore what was being sent to the effluent plant
How had the maintenance team been operating?
- Manual data collection
- Urgent reactive maintenance in response to alarms
- 15% of time spent keeping the effluent plant running, including engineers having to sit and monitor the situation to ensure nothing went wrong
- Planned maintenance and improvements interrupted by having to respond quickly to wastewater problems
What steps did they take with RS Industria?
- Connected equipment in the effluent plant, even legacy devices, to the RS Industria platform to collect data
- Created a dashboard giving real-time information on pH trends, flow rates, chemical oxygen demand (COD) and the status of pumps and valves
- Set up real-time SMS alerts and alarms
What were the outcomes?
- Transformation in terms of effluent compliance, with significant reductions in effluent COD and strength
- Ability to respond to early warning alerts before getting out of compliance
- Less time spent on reactive maintenance, meaning more time available for planned maintenance
- Time available to investigate what was coming to the effluent plant from the factory
- The ability to identify incidents in real-time thanks to the compliance dashboard
- The ability to deal with the root cause of an issue and problem-solve to prevent it happening again
“We’re able to get time back,” said Botwright. “We’re able to reduce interruption and really focus on our core maintenance tasks, ultimately improving downtime within the factory.”
“This has enabled us to take a real step change and get buy in for the platform going forward,” he continued. As a result, although the initial focus was on wastewater compliance, “Once we put the platform in and understood and we understood how the Edge Gateway worked…we started to explore what else we can get meaningful data from.”
Challenge 2: electricity usage
What was the challenge?
- More efficient use of electricity
How had the maintenance team been operating?
- Taking manual readings from meters on a weekly basis (“useless for trying to get any meaningful data on how to improve production operations,” noted Botwright)
What steps did they take with RS Industria?
- A survey to identify existing meters that could be easily connected to a network
- Created a dashboard to monitor electricity usage within the factory and gain an understanding of what was happening
What were the outcomes?
- The data collected by the dashboard revealed that while there was no production on weekends, the site was still consuming 65% of the electricity used on production days during the week because equipment such as compressors, fridges, air handling units and conveyors were not being switched off
- The maintenance team shared the data with other teams to demonstrate the advantage of turning devices off
- Targeted measures to switch equipment off reduced usage from almost 7,000 kWh on weekends to 1,800 kWh, cutting the electricity bills by 14% within a month
- When anomalies appear in the data, the cause is now investigated
Challenge 3: oil consumption
What was the challenge?
- The site is in a remote location therefore the factory uses oil for steam generation
- There’s a huge cost to turning oil into steam
- No measure of efficiency
How had the maintenance team been operating?
- Measuring the number of road tankers per month
What steps did they take with RS Industria?
- Investigated what metering was already in place but wasn’t being used
- Identified how they could put other boiler efficiency measurements in place, adding fuel meters where needed at a cost of £1,500 per boiler
- Put in place a dashboard that gave real-time information about the plant’s performance
What were the outcomes?
- The data showed that one boiler was operating less efficiently than the other because of a problem with the burner
- Within a week, a specialist engineer reconfigured the burner so this boiler was as efficient as the other – saving £5,000-£6,000 in fuel
- When presented with data to show that both boilers were now more reliable, the senior leadership team agreed to the recommendation from maintenance that one boiler be stood down for three months to save significantly on fuel
Challenge 4: chilled water
What was the challenge?
- Like many food production facilities, the site uses a lot of chilled water to cool products after they’ve been cooked
- The company was also spending around £35,000 per year to hire additional chillers to top up the fridge loading capacity during peak times
How had the maintenance team been operating?
- No data was collected
What steps did they take with RS Industria?
- Created a plan about how to monitor temperatures on the flow and return of each compressor in the route
What were the outcomes?
- The maintenance engineers soon identified a couple of troublesome areas with huge loadings at certain times
- In one instance, this was because an operator hadn’t followed standard operating procedures and therefore the system was trying to heat and cool at the same time. The data helped the team to demonstrate to those working in production about correct procedures and, crucially, why they are important
- In another instance, the problem was a software issue that maintenance could quickly resolve
- Maintenance was also able to resolve the demand for extra refrigeration facilities by using graphs showing the data when talking to the production team about timing of runs and the impact of that. As a result, loading is now smoothed out and “so far, we haven’t needed any of that additional rental capacity, which is fantastic, a really big win for us,” added Botwright
A journey of discovery
This has all been achieved without Botwright having to request capital expenditure.
“One of the big advantages of the way that the RS Industria platform operates is that I’ve been able to do this on my maintenance budget,” he told the audience. While he’s needed to make savings in some areas to pay for outlay, this investment has paid off. “Over the year to date so far, we’ve generated about £200,000 worth of savings – and there’s a lot more to go.”
Another advantage is that the configuration allows for organic growth. “We’ve identified some of the low-hanging fruit…but we’re just starting to scratch the surface,” he continued. “Our next project is on one of our vertical form, fill and seal machines…[This] isn’t necessarily around saving money, but it is very much around improving production efficiency and improving quality.”
“How have we changed?” he asked in conclusion. “Ultimately, by using the platform, we change the way that we think and use data…For a lot of engineers, data provides insight that then you can act with. For us, it’s been a discovery.
“From starting with myself and a very small amount of the team, I now have a number of users within the factory who aren’t engineers who will go in and they’ll look at the data and they’ll start to understand what’s happening because they’re keen and they want to help influence and change for the better.
“The RS platform has really given us that strong foundation to build and to move forward with.”
Find out what the founder and Managing Director of RS Industria, Richard Jeffers, shared with delegates at the Manufacturing and Engineering Week 2023 trade show