Measurement Means Money - Manufacturing & Engineering Week 2023.
3 min read
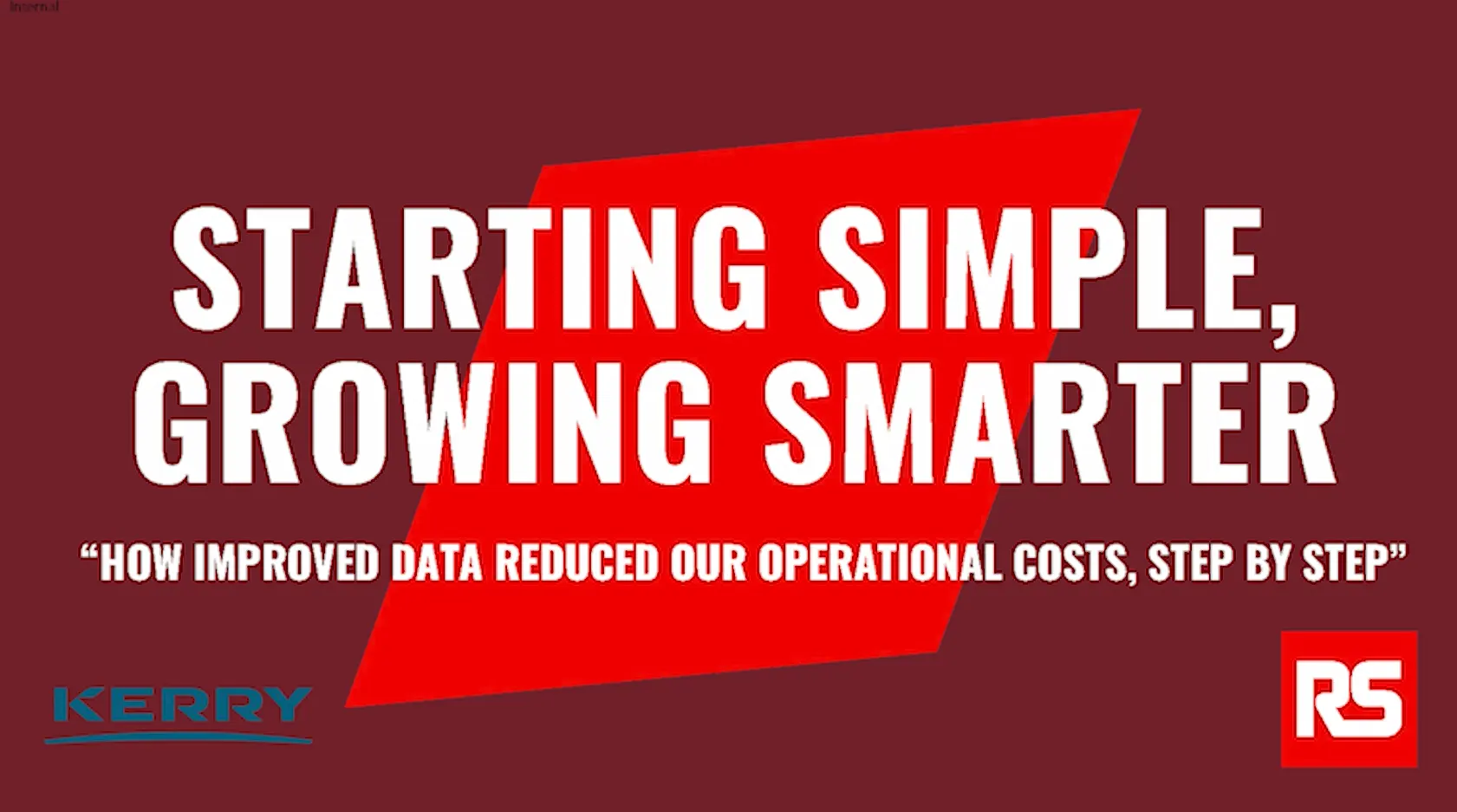
Access data, analysis data, act on data Founder and Managing Director of RS Industria, Richard Jeffers, explains the measurement means money equation.
“It’s all very well doing digital transformation and getting more data, but if it doesn’t translate into pound notes somewhere in your organisation, there’s really not much point in doing it,” stated Richard Jeffers, Founder and Managing Director of RS Industria, a modular Industrial Internet of Things (IIoT) platform, at the outset of his address at the recent Manufacturing Digitalisation Summit.
The purpose of digital transformation and data gathering is, Jeffers proceeded to argue, to gain insights into your operations – and then, crucially, make cost-saving improvements based upon those insights.
Here’s what Jeffers had to say at the summit, which formed part of the Manufacturing and Engineering Week 2023 trade show held at the NEC in Birmingham, about data, analysis and action.
Aim for efficiency
“Data is critical in driving activity in any organisation,” Jeffers told the audience. “We need data to help us understand where things are going wrong and why things are going wrong.”
However, while maintenance engineers may be accustomed to responding to sporadic events such as machine failure, there is also huge value in data that illuminates systemic issues – what Jeffers calls chronic losses.
“Every operation I've ever worked in suffers from a high level of chronic losses as well,” he explained. “And these are losses that just become accepted as the way of operating…People accept the fact that there’s 20% downtime on their packaging line. They accept the fact that their boiler house efficiency is only 79%. These become invisible.
“Those invisible losses have a massive impact on the cost of manufacturing.”
Jeffers illustrated this using evidence from newly published research produced by the Institution of Mechanical Engineering (IMechE) in partnership with RS. The Industry in Motion: Maintenance Engineering Report 2023, based upon a survey of 700 IMechE members in the UK and Ireland, reveals that manufacturing facilities experience twenty hours of unplanned downtime per week at an average cost of £5,000 per hour – a total of £100,000 of lost time and lost value each week.
“That’s the saving,” said Jeffers, “It’s about eliminating that loss.”
Access existing information
Jeffers then turned to a customer case study to demonstrate how taking measurements is a vital step in reducing or even eliminating such losses.
When the team from RS Industria began working with this food production facility, they started by looking at wastewater management. Although the site’s maintenance engineering lead “was having significant challenges in terms of regulatory compliance” in this area, “all the data that he needed to respond to that in a productive fashion was already inside his battery.
“It just wasn’t in the hands of the people that needed to make decisions based on that data,” continued Jeffers, “so our first project was to get all that wastewater data and allow his technicians to respond very quickly to that.”
This situation was mirrored in terms of electricity consumption too, with unconnected meters measuring usage but not able to share that information. “We helped in extracting all the data we already had about his electricity consumption, and a little bit of additional enrichment to that data, and brought it into our cloud platform,” said Jeffers, “allowing people to interact with that data on a daily basis.”
Act on those findings
Why did this make a difference?
“Through changing the way they operated in terms of their management processes, to getting the right people to look at that data on a daily basis, they were able to get much greater insight into how the factory was operating, and how the consumption of power was turning into volume.
“What they did was change the way they ran the factory based on some pretty simple data, and some pretty simple analytics, and delivered some pretty impressive energy reduction, 14%, and created a cultural change of caring about energy consumption.”
Jeffers also shared another case study in which the data was present within a machine but not being analysed or acted upon. As a result, this equipment was creating a bottleneck in production.
“Again, the data was already there inside that machine,” he said, “just that data was not in the hands of the people who needed to do the work.”
Accessing the data and running some basic analytics on it allowed the maintenance team to reduce the time involved in that operation – with significant results. “That improvement in cycle time has directly translated into improved output from the factory, which has translated clearly into a huge amount of value for that business.”
Don’t delay any longer
Jeffers offered advice to maintenance engineers seeking to make similar improvements.
“Time is money here. You can spend weeks, months, or years debating should we go out and measure stuff but every day you delay making a decision about collecting data, and every day you delay responding to that data, you’re losing money.
“Start small start with your big losses, where you can actually see this is a big asset costing me loads of money. Let’s start measuring – and let’s start taking action on the back of that measurement.
“Once you start measuring, you’re going understand your business and your operation better. You’re going to highlight the opportunities that exist inside your factory to drive improvement. That’s going to lead to lower waste, higher profits and ultimately a stronger and more resilient business.”