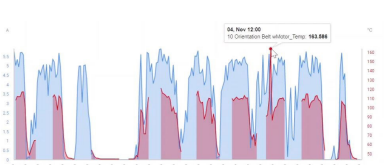
By generating insights from conveyor belt data, RS Group’s Nuneaton distribution centre created all-new value with a simple installation of RS Industria.
The Challenge
RS Group is a vast global operation, distributing more than 500,000 industrial and electronic products around the world.
Sourcing products from over 2,500 leading suppliers with operations in 32 countries, the company provides a wide range of value-added solutions to over one million customers. This includes shipping over 50,000 parcels every day via multiple distribution channels.
Its biggest UK distribution centre for delivery processing is based at its Nuneaton Regional Distribution Centre (RDC).
With 650 employees working on-site, this Centre features over 10km of automated conveyors, 28 automated cranes, three Dematic sorters and two automated packing machines that enable over 26,000 customer orders to be processed every day.
Preventing downtime is essential to protect operational efficiency and keep the Centre running cost-effectively.
The Solution
Ensuring all machinery remains functional is a critical task and, having developed its RS Industria IIoT platform in-house, it was only natural for the RS Group to put this technology to use within its own Nuneaton RDC to perform asset monitoring.
In particular, RS Industria was used to simultaneously monitor all 65 conveyor drives on the FPF sorter. With three induct belts loading items onto the main conveyor stream, the sorter is able to process over 1,500 orders per hour.
The Journey
The conveyor was operating as planned until, one day, the RS Industria system triggered an automatic alert. This was for an induct belt drive that conveys parcels onto one of the four main conveyors.
This particular induct conveyor has to load over 400 items onto the sorter every hour, with the sorter processing upwards of 3,000 items in that time. If one of these belt drives fails, it means that all the items on that belt have to be manually transferred to another induct. This not only impacts the capacity of the entire sorter, but manual intervention of this nature can incur additional labour costs of up to £500 per hour.
The automatic alert indicated that the current of the conveyor drive was well above the upper limit. In this particular conveyor design, the induct belt that feeds packages onto the main belt is angled. This means that it has to be fed through a number of rollers to change its shape at one end. These rollers add friction to the belt, which can quickly build into a high load for the drive motor. However, having checked the conveyor and with everything appearing to be working, the on-site team assumed all was well.
However, the RS Industria system continued to send alerts, indicating there was an ongoing problem.
Examining the alert data in more detail using RS Industria’s online dashboards, the current spikes (blue on the graph) and the drive’s temperature (red on the graph) revealed that it was clearly under excessive load. This was causing the motor to overheat, with the temperature peaking at 163°C, well above the recommended operating limit of 90°C.
If this continued for much longer, the motor would surely fail. Physical examination of the drive and the conveyor belt revealed that the friction of the belt over the runners was very high, permanently creating a high running load.
Following a discussion with the on-site maintenance team, it was revealed that the belt on this conveyor had recently been changed. However, the replacement belt was a different specification, being marginally thicker and the rubber slightly harder than the original.
Changing the belt to the original specification solved the overloading and overheating problem, and the current and temperature returned to normal operating limits.
The Outcome
If this problem was not discovered early enough, it would have led to failure and costly downtime.
Additional costs include the manual work that would be required to transfer all the items from the failed conveyor to another conveyor line. The incident certainly raised the team’s awareness of the critical nature of this conveyor, and they are now working on ‘engineering out’ the risk of belt failure by upgrading the unit to a multi-belt type.
The use of multiple thin belts on multiple rollers will enable the unit to continue operating even if one or two belts break.
Installing the RS Industria system for asset monitoring was quick and easy, with insights being provided almost immediately. This simple installation of IIoT goes to prove just how much value can be generated from the right data.
With these benefits gained, the modular system can then easily be expanded to other areas of the factory.
Ready to learn more?
Read on to ‘The steps and skills required for an IIoT implementation’.