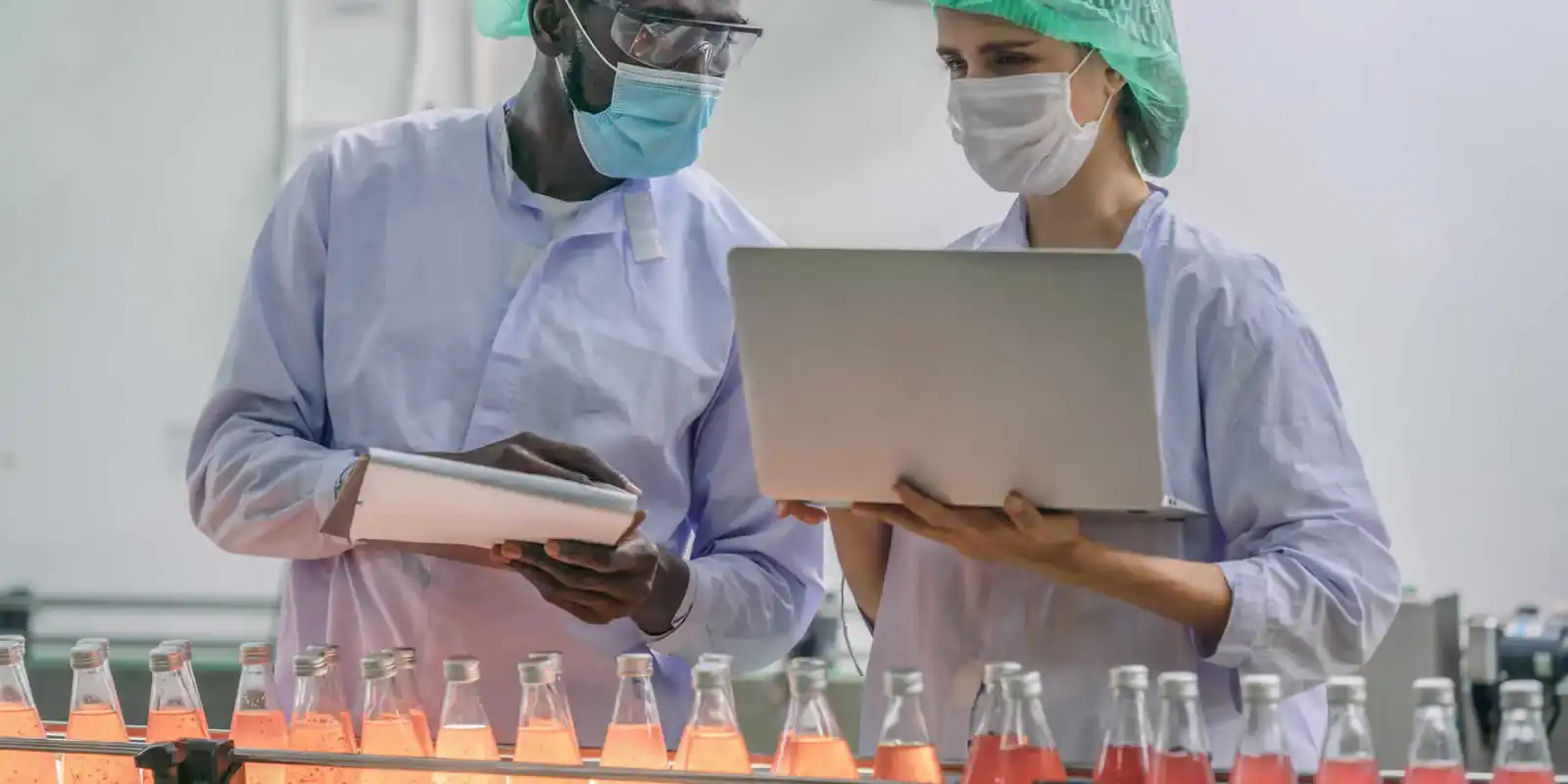
Continuous improvement to cut waste and better manage asset reliability is at the heart of every successful maintenance strategy.
For the food and drink industry, being able to prevent unplanned stoppages and costly downtime by monitoring asset performance keeps machines moving smoothly, and products on the shelves.
For Refresco, the UK’s largest drinks and contract packing manufacturer, effective operations mean the company can deliver on its aim to get its ‘drinks on every table.’
The global Refresco Group is the world’s largest independent bottler. Its UK arm employs more than 1800 staff at six processing facilities across Scotland, England, and Wales, including its Bondgate site in Pontefract, West Yorkshire.
As Refresco’s largest canning site in the UK, Bondgate is home to four canning lines, capable of manufacturing more than 750 million cans per year. This includes big-name and private-label energy drinks and ready-mixed alcohol beverages.
Improving performance
To ensure customers get the best quality products, Refresco recognises the importance of agile culture and regular investment into its operations. It’s also a pioneer of manufacturing excellence.
At Bondgate, engineers roll out initiatives that improve performance, working together to resolve any issues quickly.
It is an approach that requires high-quality machinery and the support of like-minded, innovative supply partners like RS Industria to keep them moving. By working together, RS Industria provides Refresco with clever and detailed insight into the inner workings of both legacy and new assets.
High-speed can fillers and seamers are key to Bondgate’s operations and fulfilling the demands of the supply chain. As highly complex rotating assets, spares for these multi-million-pound machines are costly. In the case of the main bearings, supply lead times can run into months as they are typically manufactured to order.
Capable of operating at 1500 cans/per minute, the high-speed can filler and seamer on Bondgate Line 4 is one of the most utilised fillers at the plant.
Now out of the manufacturer’s standard year-long service package, the engineering team at Refresco would have to take over ongoing maintenance of the critical asset.
In parallel, engineers keen to move from reactive maintenance to a planned and predictive culture needed a way of being able to monitor potential degradation of the filler’s rotational elements.
The answer is the right technology
The answer? RS Industria. Using the right monitoring technology to ensure that all main failure modes are detected, RS Industria gives visibility where there is none, knitting together insight into a single overview and alerting engineers to any risk of failure.
14 individual accelerometers were installed on the main rotating components, with the sensors connected to RS Industria’s onsite Edge Gateway via vibration monitoring cards.
A customised real-time dashboard was created to give the engineering team complete insight into vibration data for each system. If any of the vibration levels were to be exceeded, an automatic alert would be triggered and sent to the engineers via text and email.
Within weeks of RS Industria’s use on the can filler, it kicked into action, revealing abnormal vibration levels on the main bearing ring. When the line was shut down for investigation, it revealed the critical component was being starved of lubrication due to a blocked grease line.
Had the machine continued to run, irreparable damage would have been caused and the machine would grind to a halt. The cost? A minimum of £100,000 for replacement parts, repair, and associated labour.
RS Industria saves customers time and money, time and again. If you’re looking to turn reactive maintenance on its head, it’s time to give us a call.